Application
The applications of tungsten carbide that follow are about nearly every aspect of the manufacturing industry, from metal cutting to mold industry, oil&gas to mining&engineering, wire industry to nail industry, refractory to construction and so on.
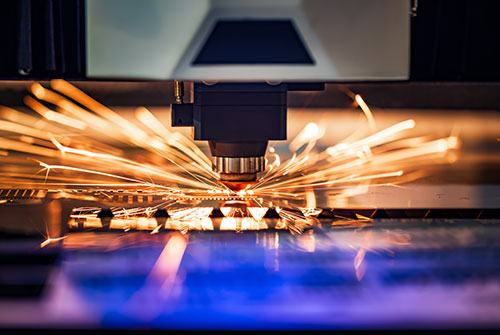
Metal cutting
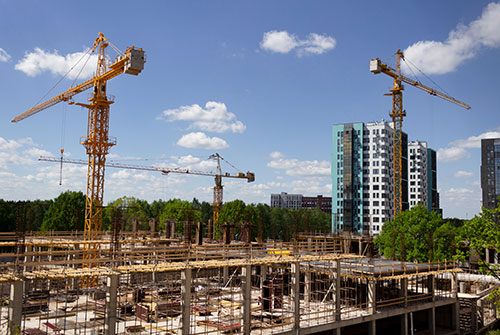
Construction
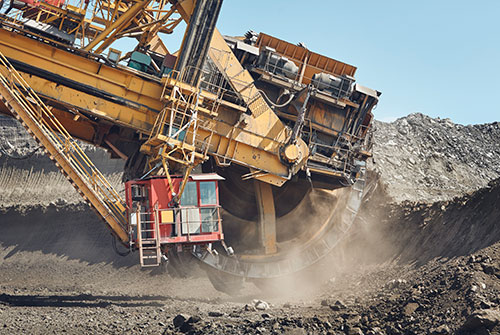
Mining and Engineering
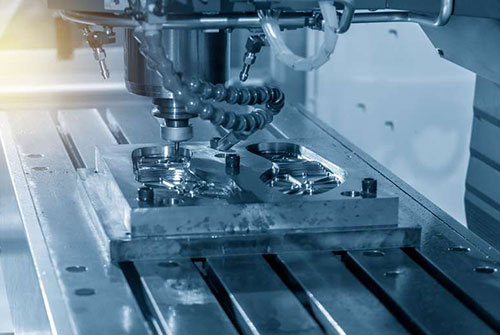
Mold Industry
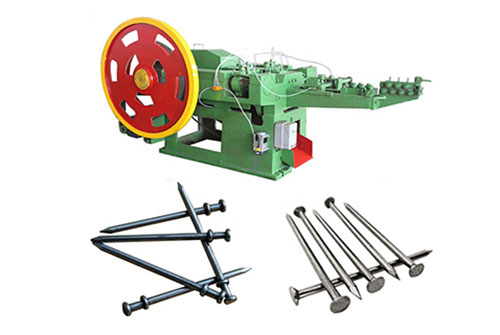
Nail Making
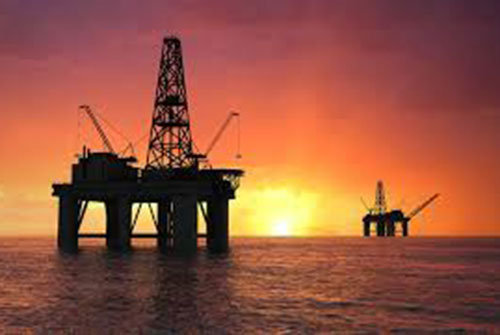
Oil and Gas
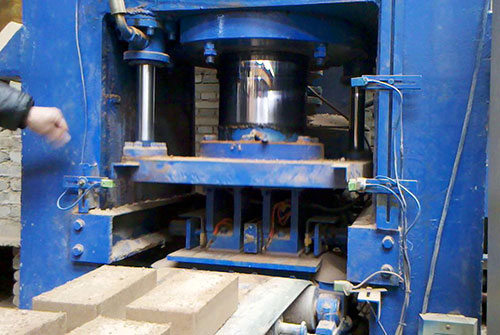
Refractory
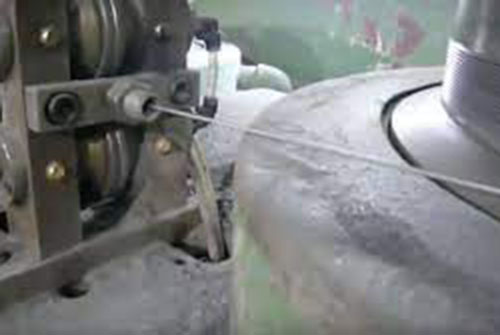
Wire Drawing
Tungsten Carbide Blanks
We manufacture a lot kinds of tungsten carbide blanks, including carbide strips, wire drawing dies, tungsten carbide plates, carbide nozzles, carbide washers, carbide buttons and so on, etc. They are mainly used in metal cutting, mold industry and so on.
Custom Carbide Products
Custom carbide products are our company strong points. We are producing lots of the items based on customers’ drawings and exact requirement, such as pelletizer knife, carbide cutters for wood turning, carbide eyelets, carbide nails dies, carbide valve seat, etc. These items are having good performance on oil&gas, wire industry and mail industry, cutting and so on.
Brazing carbide products
Brazing carbide products are our company newly developed, contains wear liners, brazed liners for refractory brick mold, carbide liners for ceramic tile mold, VSI crusher parts and crusher blades. They are taking important role in mining and engineering, refractory, construction and so on.
Carbide Terminology
Tungsten carbide, a remarkable material, is forged through the amalgamation of powdered metals like tungsten, cobalt, and carbon, sintered at incredibly high temperatures. In contrast, cemented carbide is an amalgam produced by the reaction between carbon and tungsten powder, also at elevated temperatures. Tungsten carbide, an amalgamation of tungsten (symbol W) and carbon (symbol C) atoms, boasts exceptional hardness, durability, and a high melting point. Its notable attributes include remarkable resistance to wear and corrosion. Tungsten carbide finds extensive application in diverse industrial sectors, where the demand for hardness and toughness is paramount.
The chemical formula for tungsten carbide is WC, symbolizing an equal proportion of tungsten and carbon. Its fabrication usually involves a powder metallurgical process that entails the fusion of tungsten powder and carbon black at elevated temperatures, typically ranging from 1500 to 2000 degrees Celsius. This process is facilitated by introducing a binder metal like cobalt. The resulting compound manifests as a rigid and brittle material.
Cemented carbides can be categorized into various types:
Based on composition: tungsten cobalt carbide, tungsten titanium cobalt carbide, tungsten titanium carbon carbide, and more.
Based on application: cutting carbide, mining tool carbide, oil drill carbide, construction tool carbide, and others.
Based on granularity: super grain carbide, sub-grain carbide, normal grain carbide, and others.
Grade
Tungsten carbide is typically available in a variety of grades, with each grade representing a distinct chemical composition and set of performance characteristics. These grades are often denoted by alphanumeric codes, such as ISO K10, ISO K20, ISO P30, and so on. They serve to identify crucial aspects of the carbide, including the tungsten carbide particle content, particle size, bonding phase content, and the type and quantity of additional additives.
It is important to note that different manufacturers may adopt different grading systems for carbides. Therefore, when choosing and comparing carbides, it is essential to have a thorough understanding of each manufacturer’s grading system and its corresponding performance attributes.
Here are some commonly encountered grades:
Tungsten-Cobalt Carbide: This carbide comprises WC and Co, with grades typically designated by the prefix YG, such as YG6, YG8, YG15, and so on. For instance, YG6 indicates that the mass fraction of tungsten in the tungsten-cobalt cemented carbide is 94%, while the mass fraction of cobalt is 6%.
Tungsten-Cobalt-Titanium Carbide: Comprised of WC, TiC, and Co, this carbide is usually denoted by the prefix YT, such as YT5, YT15, YT30, and others. For example, YT5 signifies that the mass fraction of tungsten in the tungsten-cobalt-titanium carbide is 85%, the mass fraction of cobalt is 10%, and the mass fraction of titanium is 5%.
Tungsten-Titanium-Carbon Carbide: This carbide is created by incorporating TaC (or NbC) alongside WC, TiC, and Co. The addition of TaC (or NbC) enhances the overall performance of the carbide. Its grades typically begin with YW, such as YW1, YW2, YW3, and so forth.
Distinct carbide grades exhibit variations in terms of tungsten carbide particle content, particle size, binder phase content, and additive types. These disparities directly impact the hardness, wear resistance, and toughness of the carbide. Consequently, selecting the appropriate carbide grade becomes crucial for specific applications and requirements. When making the right choice, it is essential to balance the relationship between hardness, wear resistance, and toughness, while considering the specific demands of the application, in order to achieve an optimal fit in terms of performance and lifespan.
Density
Density is the mass of a substance per unit volume and is used to describe the compactness of a tungsten carbide material. The density of tungsten carbide typically ranges from 13 g/cm3 to 15 g/cm3.
The test method uses the drainage method (Archimedes’ principle) to measure the density. The density of cemented carbide is more sensitive to composition and porosity. With constant composition and porosity, the density decreases as the carbon content increases. By comparing the precisely measured density values with those in the ideal state, changes in the internal organisation and composition of the material can be detected.
Hardness
Hardness denotes the capacity of a substance to withstand partial scratches or indentations, serving as a fundamental gauge of its overall sturdiness. It mirrors the material’s resilience against scratching, erosion, and distortion. The hardness of tungsten carbide is typically evaluated through two approaches: Rockwell hardness and Vickers hardness.
Rockwell hardness involves subjecting the material’s surface to varying levels of pressure and subsequently measuring the depth of the resultant indentation. It is denoted by HRA, HRB, and HRC, with HRA indicating greater hardness for harder substances, HRB for moderately hard substances, and HRC for softer materials. A higher numerical value signifies heightened hardness.
On the other hand, Vickers hardness entails the precise application of pressure to the material’s surface, followed by measurement of the diagonal length of the resulting indentation. Vickers hardness is commonly expressed as HV, where increased values correspond to augmented hardness.
Bending Strength(TRS)
Bending strength (Transverse rupture strength) is the maximum stress or load that a material can withstand without damage when subjected to a bending load. It is a measure of the resistance and toughness of a material under bending loading. Bending strength is usually expressed using megapascal (MPa) in the Standard International System of Units (SI), with megapascal indicating the force per square metre withstood.
Tungsten carbide typically has a high bending strength and can withstand high bending stresses without damage. In general, the bending strength of tungsten carbide ranges from 1000 MPa to 2000 MPa. This is a general range and the exact value may vary depending on the material formulation and preparation process.
Measurement of the bending strength of tungsten carbide is usually carried out using the standard three-point bending test method. In this test, the sample is supported on two fixed pivot points and a force is then applied in the middle of the sample to cause it to bend. By measuring the deformation of the sample and the change in force, the bending strength can be calculated. This test method provides an assessment of the ability of the tungsten carbide to resist bending loads in practical applications.
Porosity
Porosity is the proportion of volume occupied by pores or voids within a material. Porosity is one of the important parameters in assessing the denseness and quality of a tungsten carbide material.
During the manufacture of tungsten carbide, the particles and the bonding phase are bonded together by sintering or fusion. However, due to physical and chemical factors during the preparation process, some pores or voids may form within the material. The size of the porosity directly affects the properties of the tungsten carbide. Higher porosity results in a material with reduced strength and toughness, wear resistance and impact resistance. It is important to reduce porosity in order to obtain a high quality carbide material.
Measuring the porosity of tungsten carbide can be achieved using different methods such as the gas emission method, mercury pressure method or image processing techniques. These methods allow porosity to be calculated by measuring the volume and effective volume of the material.
Magnetic Saturation (Cobalt magnetisation)
Coercive Force (HC)
The sample reaches the saturation magnetization state in the magnetic field, and then the size of the reverse magnetic field required to make the sample lose all magnetism (M=0) is the coercive force to be measured. It is a non-destructive testing method that reflects the average grain size and uniformity of the alloy.
Detecting the coercive force of cemented carbide can evaluate the magnetic properties and particle size distribution of the material, so as to judge the quality and performance of cemented carbide. The size of the coercive force is related to the particle size, interaction force, crystallinity and other factors in the cemented carbide, so it can be used to optimize the preparation process and material composition of the cemented carbide. In application, the coercive force of cemented carbide has an important influence on its wear resistance, hardness, corrosion resistance and other properties. Higher coercive force usually means better wear resistance and higher hardness, because it means smaller particle size, higher crystallinity and stronger interaction force in cemented carbide, which improves the material strength and durability.