Carbide Brazing
Brazing carbide products are mainly used for mining, crushing, molding. As a wear part, its performance is much better that traditional wear material and cost-effective.
REQUEST A QUOTE FOR MORE DETAILS
Something You Should Know about Carbide Brazing
What is the brazing of cemented carbide and steel
The rapid development of the manufacturing industry has increased the demand for various products made of cemented carbide. But due to the high price of cemented carbide, it is difficult to manufacture large workpieces with complex shapes using it. Therefore, combining cemented carbide with steel allows the strength and toughness of both to complement each other, creating results greater than summing up these two materials separately.
Currently, most cemented carbide is used by welding method set on medium carbon steel or low alloy steel substrate. In this way can we make full use of the respective advantages of cemented carbide and steel, greatly reducing material costs and improving performance and service life. Although welding can be carried out, it is prone to hardened structure and cracks during welding. Effective process measures must be taken to obtain satisfactory welded joints. At present, the commonly used welding methods for welding hard alloy and steel in production include oxygen-acetylene flame brazing, vacuum brazing, arc welding, inert gas shielded welding, friction welding, plasma arc welding, vacuum diffusion welding and electron beam welding.
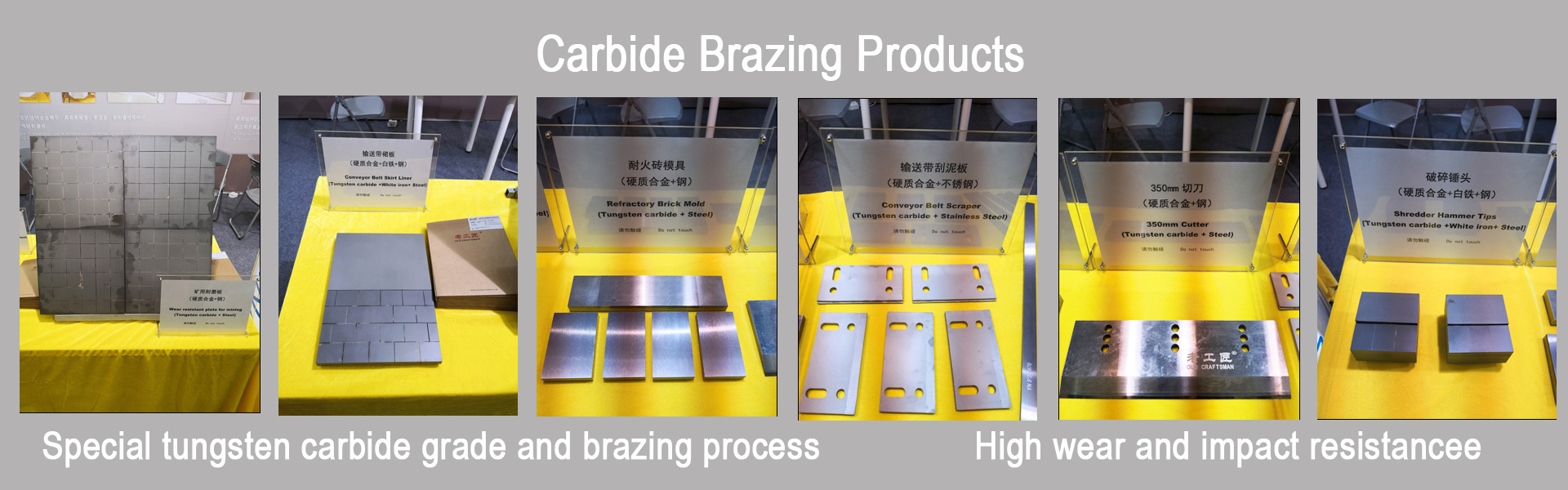
Some commonly used methods of brazing
We might first distinguish between welding and brazing: in the former the connection is made by melting the base material (the material to be welded), in the latter the base material does not melt, but the brazing material melts and penetrates the gaps between the base materials by capillary action, and the connection is made after cooling and solidification. It can be said that brazing is a form of welding. Several common high-temperature brazing processes are listed below.

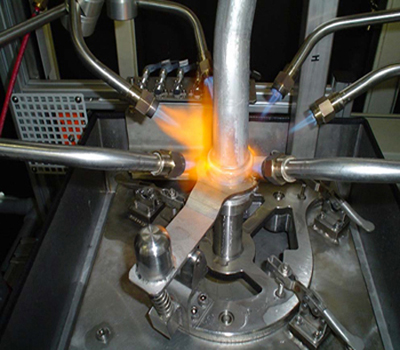
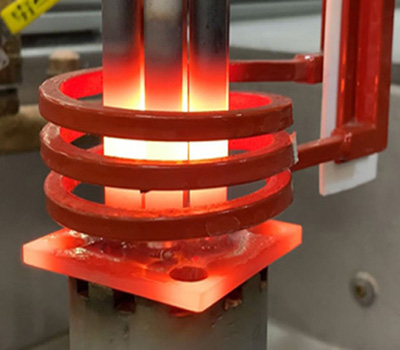
1. Induction brazing. It is a brazing method using high, medium or industrial frequency induction current as a heat source. High-frequency heating is suitable for welding thin-walled fittings. The use of coaxial cables and split induction loops allows brazing to be carried out on site away from the power source and is particularly suitable for welding certain large components, such as pipe joints on rockets that need to be dismantled. However, induction brazing suffers from a number of defects, such as poor forming accuracy, which can lead to mis-welding; the small melting area and rapid cooling of the metal during welding can easily lead to uneven distribution of the weld metal chemistry.
2. Flame brazing. Brazing is carried out using a flame of combustible gas mixed with oxygen or compressed air as a heat source. Flame brazing equipment is simple and easy to operate, and depending on the shape of the workpiece, multiple flames can be used for simultaneous heating and welding. This method is suitable for the welding of small and medium-sized parts such as bicycles, electric bicycle frames and aluminum kettle spouts.
3. Resistance brazing. Resistance brazing is a welding method in which two workpieces are placed between two electrodes, pressed and energized, and the current is allowed to flow through the workpiece so that the workpiece itself generates resistance heat to heat the workpiece and melt the brazing material. This method has the advantages of rapid heating, high productivity, concentrated heating with little thermal influence on the surrounding area, simple technology, and easy automation of the welding process. However, the size of the brazed joint must not be too large and the shape must not be too complex, which means that this brazing method is limited by the shape and size of the joint.
4. Vacuum brazing. Vacuum brazing technology is a more advanced welding method to achieve material connection without adding brazing flux under vacuum conditions. It can effectively avoid the pollution of oxygen and nitrogen gas by other welding methods and obtain a clean and dense joint with good mechanical properties and corrosion resistance, which is an important production tool for the aerospace and electrical and electronic industries. Vacuum brazing technology can effectively remove the oil and oxide film from the surface of the welded parts and promote the wetting and spreading of the surface of the brazing material, which is suitable for welding aluminum alloys, titanium alloys, high temperature alloys and other homogeneous or heterogeneous materials, but also for ceramics, graphite, cemented carbide and diamond materials.
Advantages of
Vacuum brazing
Our company chooses vacuum brazing to make welded products, mainly because it offers a range of advantages over other brazing methods.
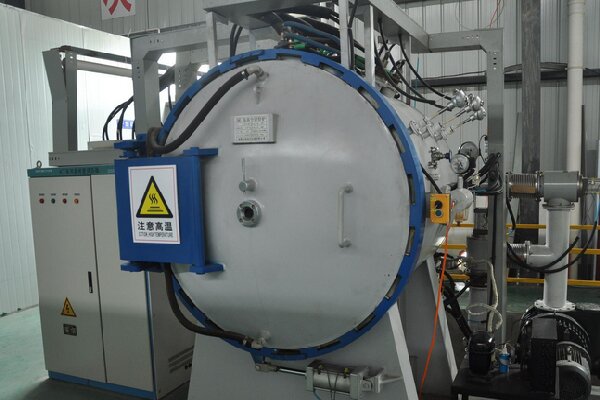
1.Vacuum brazing not only saves a large amount of expensive metal brazing flux, but also does not require complex flux cleaning processes, reducing production costs.
2.Vacuum brazing, because of using no brazing flux, it significantly improves the corrosion resistance of the product, eliminates all kinds of pollution, pollution-free processing equipment costs, and has good safety production conditions.
3.The good wetting and fluidity of vacuum brazing material makes it possible to weld more complex and narrow channel devices, and vacuum brazing improves the yield of the product and obtains a solid and clean working surface.
4.Many materials are suitable for vacuum brazing, such as: aluminum, aluminum alloy, copper, copper alloy, stainless steel, alloy steel, low carbon steel, titanium, nickel, Inconel, etc. They can be brazed in the vacuum furnace, and the designer can determine the required materials according to the use of brazing devices.
Several aspects that need attention when brazing
1. The relationship between linear expansion coefficient and brazing cracks. The size of cemented carbide is relatively small, and it is generally fixed on a relatively thick steel support material. Brazing is an effective welding method to connect cemented carbide and base metal. The linear expansion coefficient of cemented carbide (4.1~7.0×10-6/℃) is very different from the linear expansion coefficient of ordinary steel (12×10-6℃-1), and cemented carbide is only 1/3 of steel ~ 1/2 or so. Both cemented carbide and steel expand freely when heated, but the shrinkage of steel is much greater than that of cemented carbide when cooled. At this time, the welding seam is under pressure, and the surface of the cemented carbide is under tensile stress. If the residual stress is greater than the tensile strength of the cemented carbide, cracks may occur on the surface of the cemented carbide. This is one of the most important causes of cracks in cemented carbide brazing.
2. The relationship between hardness and crack sensitivity. The hardness of cemented carbide is directly proportional to wear resistance and welding crack sensitivity. The higher the hardness of cemented carbide is, the more likely cracks emerge during brazing. Moreover, the cemented carbide used for general finishing or super finishing is prone to cracks during brazing. According to the hardness and strength of different grades of cemented carbide, the welding crack susceptibility of cemented carbide can be judged. The order from poor to good is as follows.
YG category YG3X, YG3, YG4, YG6X, YG6, YG8, YG11, YG15
YT type YT60, YT30, YW1, YT15 (YW2), YT14, YT5
The above two types of cemented carbides, from left to right, show that the hardness and wear resistance gradually decrease, while the strength and toughness increase, and the possibility of brazing cracks decreases.
3. The influence of welding residual stress. The residual stress in the welding area is a potential hazard. Although cracks may not be found on the cemented carbide workpiece immediately after welding, it is easy to produce cracks in the subsequent sharpening, storage or use process. Cause the tool to be scrapped. When the brazing area of the cemented carbide is larger, the residual welding stress generated is greater, and the possibility of cracks is greater. When welding cemented carbide tools, the welding residual stress must be minimized. Measures must be taken to reduce the brazing stress during welding. Measures such as lowering the brazing temperature, preheating and slow cooling before welding, selecting brazing filler metals with good plasticity, adding compensation gaskets, and improving the joint structure can be taken. When brazing a large area of cemented carbide, no matter the strength is high or low, special measures should be taken to reduce welding stress and prevent cracks.
4. Oxidation problem. When the cemented carbide is heated to above 800°C in the air, the surface of the cemented carbide begins to oxidize, forming a loose oxide layer, accompanied by decarburization. When heated to 950~1100℃, the surface layer will oxidize rapidly, and the formed oxide film will make the cemented carbide brittle and reduce the mechanical properties. The presence of surface oxide layer also reduces the strength and hardness of the weld. Taking measures during welding to minimize the oxidation of hard alloy welding parts is an important measure to improve welding quality.