Tungsten carbide (WC) is widely regarded as the premier material for High-Pressure Grinding Roll (HPGR) wear plates due to its exceptional durability and wear resistance. Here’s a breakdown of its key advantages:
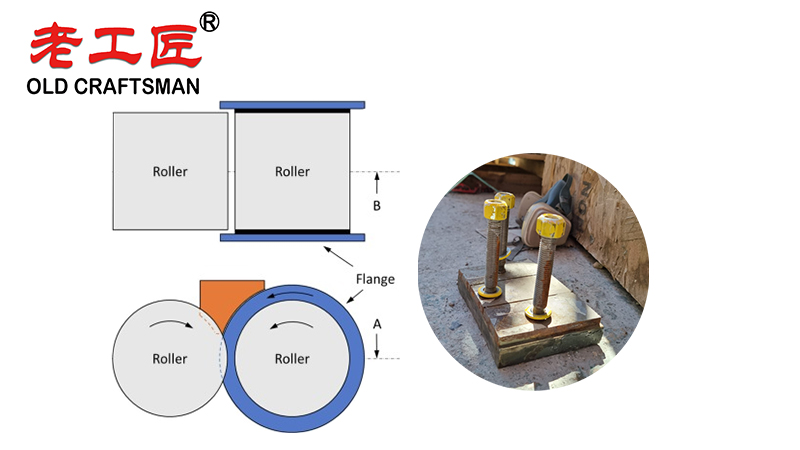
1. Extreme Hardness & Wear Resistance
- Tungsten carbide has a Vickers hardness of 1,500–2,400 HV, far exceeding hardened steel (~800 HV) and even some ceramics.
- This hardness minimizes abrasive wear from ore particles, significantly extending service life compared to conventional materials.
2. High Compressive Strength
- WC can withstand compressive stresses exceeding 6,000 MPa, making it ideal for HPGRs, which operate under extreme pressures (50–300 MPa).
- Unlike steel, which can deform under load, tungsten carbide maintains structural integrity, reducing maintenance downtime.
3. Superior Fracture Toughness (Compared to Ceramics)
- While WC is brittle compared to metals, modern cobalt-bonded tungsten carbide grades (e.g., WC-Co) offer improved toughness (up to 20 MPa√m), resisting cracking under cyclic HPGR loading.
4. Corrosion & Oxidation Resistance
- WC-Co grades resist chemical wear from moist or acidic ores, unlike steel, which can corrode or spall.
- Protective coatings (e.g., CVD/PVD) can further enhance corrosion resistance in harsh environments.
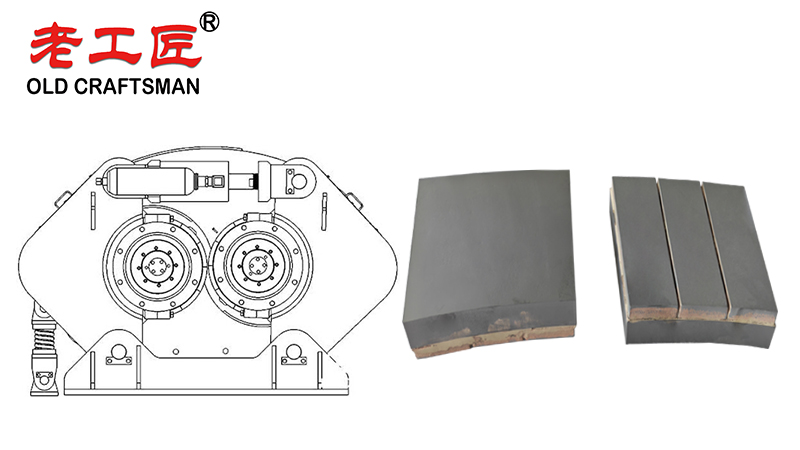
5. Economic Long-Term Benefits
- Although initial costs are higher than steel, WC wear plates last 3–10x longer, reducing replacement frequency and downtime.
- Lower total cost of ownership (TCO) due to reduced labor and machine stoppages.
Comparison to Alternatives
Material | Hardness (HV) | Compressive Strength (MPa) | Wear Life (Relative to Steel) |
---|---|---|---|
Tungsten Carbide | 1,500–2,400 | >6,000 | 3–10x |
Hardened Steel | 600–900 | 2,000–3,000 | 1x (Baseline) |
Ceramics (Al₂O₃) | 1,500–2,000 | 3,000–4,000 | 2–5x (but brittle) |
Key Applications in HPGRs
- Roll studs
- Wear plates & liners
- Feed hoppers
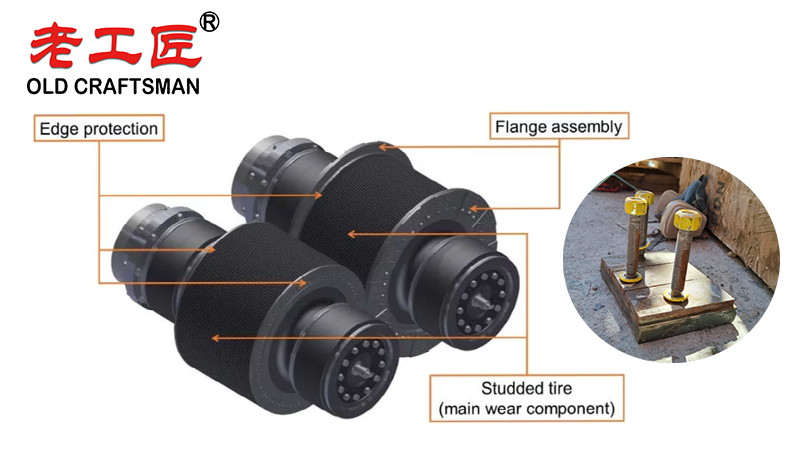
Conclusion
Tungsten carbide’s unmatched hardness, compressive strength, and wear resistance make it the optimal choice for HPGR wear components, ensuring longer operational life, reduced maintenance, and higher cost efficiency in mineral processing.
By implementing these advanced tungsten carbide wear plate solutions, mining operations can significantly improve HPGR performance while reducing total cost of ownership through extended service life and improved operational efficiency.
“Zhuzhou Old Craftsman Precision Alloy Co., Ltd. could make tungsten carbide wear parts and make your equipment use life is tens of times longer than before! We specialize in providing customized carbide wear products solutions to meet the demanding requirements of industries such as aerospace, automotive, mining, and precision machining.”