Tungsten carbide wear parts are critical in refractory brick molds due to their exceptional hardness, wear resistance, and durability under high-temperature and abrasive conditions. These properties make them ideal for enhancing the performance and lifespan of molds used in producing refractory bricks for industries like metallurgy, cement, glass, and chemicals.
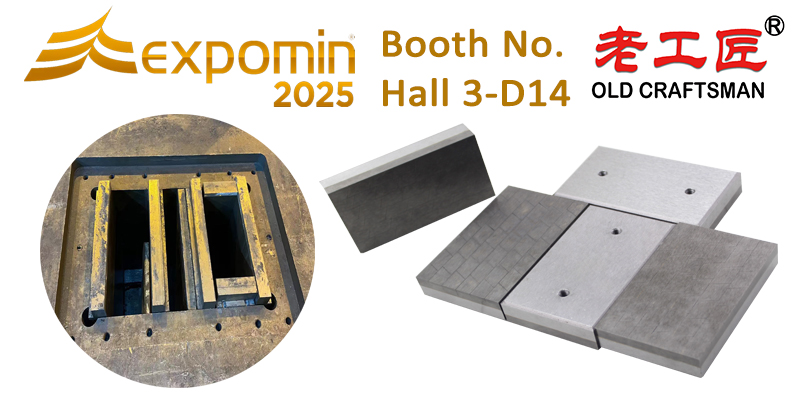
Key Applications and Benefits:
Tungsten Carbide Liners and Inserts:
- Function: Liners or inserts are brazed onto steel mold templates to form wear-resistant surfaces. They withstand the intense abrasion and pressure of pressing refractory materials like alumina (Al₂O₃) or silica.
- Advantages:
- Extended Service Life: Compared to traditional materials like hardened steel or cast iron, tungsten carbide liners can press significantly more cycles (e.g., up to 15,000 presses or 540 tons of Al₂O₃ before needing regrinding).
- Higher Precision: Maintains dimensional stability, reducing defects in brick production.
- Reduced Downtime: Less frequent mold repairs or replacements save costs.
- Crack Resistance: Customers report fewer cracks and chips in molds with carbide liners.
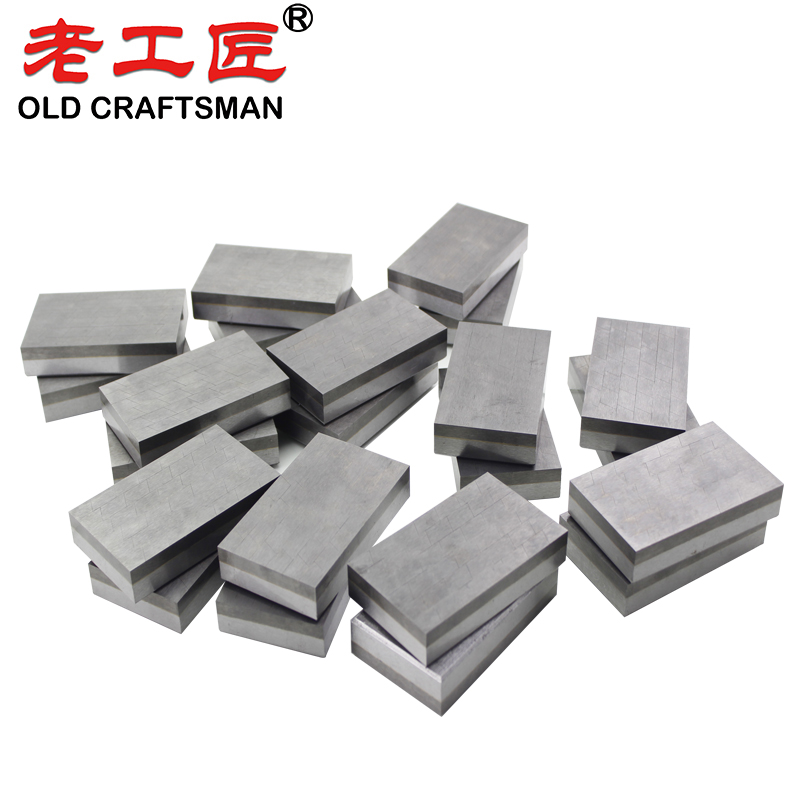
Types of Wear Parts:
- Brick Mold Liners: Fully protected with tungsten carbide or carbide/ceramic tile arrangements for mixers, Sand Muller Plows, or crushers.
- Carbide-Tipped or Full-Face Parts: Used in dies, scrapers, and other components exposed to high wear.
- Customized Plates and Tiles: Tailored for specific mold designs, often with vacuum-brazed carbide tiles for secure bonding and minimal stress.
Material Properties:
- Composition: Tungsten carbide (WC) is a composite of tungsten and carbon, often with cobalt (6-20%) as a binder for added toughness.
- Hardness: Comparable to corundum, with a Rockwell A hardness of ~92, making it resistant to scratching (only diamond abrasives can cut it).
- Wear Resistance: Outperforms steel by 2-3 times in rigidity and wear resistance, ideal for abrasive environments.
- Thermal Stability: Maintains hardness at temperatures up to 500°C, suitable for high-temperature refractory processes.
- Low Thermal Expansion: Ensures dimensional stability during repeated heating cycles.
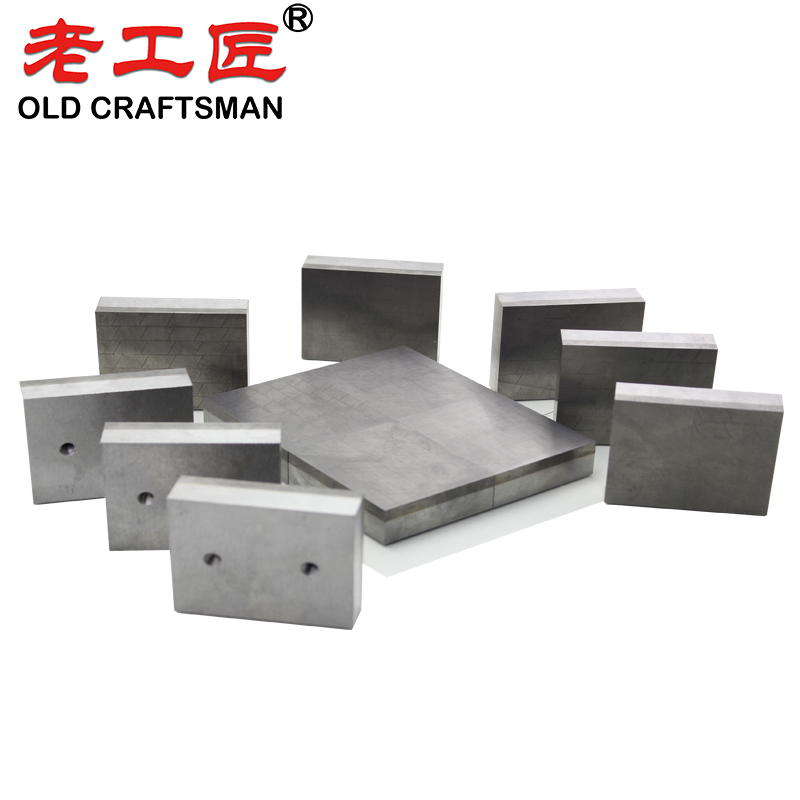
Manufacturing Techniques:
- Powder Metallurgy: Tungsten carbide parts are sintered at 1,400–1,600°C, binding WC particles with cobalt or nickel for strength.
- Vacuum Brazing: Advanced brazing techniques reduce internal stress and ensure strong adhesion of carbide tiles to steel backings, improving durability.
- Precision Machining: CNC machining achieves tight tolerances (up to 0.001mm) for complex mold geometries.
Evolution of Mold Materials:
- First Generation: Used modified cast iron or low-carbon steel (e.g., A3, 45# steel) with heat treatment (HRC 60-64). These were low-cost but had short lifespans.
- Second Generation: Tool steel or high-carbon steel extended life slightly but lacked cost-effectiveness.
- Third Generation: Tungsten carbide with steel backings offers superior longevity, precision, and wear resistance, despite higher initial costs.
Industry Applications:
- Metallurgy: Molds for furnace walls, bottoms, and doors in steelmaking or ironmaking furnaces.
- Cement: Produces bricks for kiln walls and clinker furnaces.
- Glass Manufacturing: High-precision molds for glass kiln bricks.
- Chemical and Refining: Molds for reactors, heat exchangers, and distillation towers.
Challenges and Considerations:
- Cost: Tungsten carbide is 2-3 times more expensive than hardened steel, with lead times up to 8 weeks for custom parts.
- Oxidation at High Temperatures: Above 600°C in aerobic environments, tungsten carbide can form porous oxide layers, reducing strength and surface quality. Protective coatings or controlled environments (e.g., vacuum or nitrogen) mitigate this.
- Brazing Quality: Poor brazing can lead to carbide tile breakage or cracking. Advanced vacuum brazing improves reliability.
- Skilled Labor: The refractory mold industry faces shortages of skilled workers for precision manufacturing.
Innovations and Trends:
- Customizable Designs: Manufacturers like Zhuzhou Old Craftsman and Titan Machinery offer tailored carbide liners and inserts to meet specific client needs.
- Hybrid Materials: Combining carbide with ceramic tiles or steel backings enhances performance while balancing costs.
- Surface Treatments: Carbonitriding and mirror-finish polishing reduce wear and improve mold release.
- Sustainability: Longer-lasting carbide molds reduce waste and replacement frequency, aligning with environmental regulations.
Conclusion:
Tungsten carbide wear parts revolutionize refractory brick mold performance by offering unmatched durability, precision, and wear resistance. While initial costs are higher, the long-term savings from reduced downtime, fewer replacements, and improved brick quality make them a valuable investment. For specific applications, partnering with manufacturers like Kinton Carbide or Zhuzhou Hongtong, who provide customized solutions and advanced brazing techniques, ensures optimal results.
Looking Forward to EXPOMIN 2025
EXPOMIN 2025 is a fantastic opportunity for us to connect with the mining community, share our expertise, and explore new partnerships. We are particularly excited to engage with clients and partners in Chile, a country at the forefront of the global mining industry. Join us in Santiago to discover how ZZ OLD CRAFTSMAN can help you achieve greater efficiency, sustainability, and profitability in your mining operations.
Stay tuned for more updates as we prepare for EXPOMIN 2025. Follow us on ZZ OLD CRAFTSMAN Social Media Links, for the latest news and insights from our team. We can’t wait to see you in Santiago!
Blet scarper Brazing brazingprocess CARBDIE HAMMER carbide Carbide belt scraper carbidebrazing carbide hammer Crusher CRUSHER HAMMER Informational Internal stress metal mining mold operate Refractory Brick Mold Secondary belt cleaner scraper stresses VSI VSI crusher wear plates welding work