Tungsten carbide (WC) wear parts are critical components in mining crushing applications due to their exceptional hardness, wear resistance, and durability under harsh operating conditions. Vacuum brazing is a preferred joining technique for attaching tungsten carbide to steel substrates, enhancing the performance and longevity of wear parts like crusher jaws, cones, hammers, grinding rolls, and conveyor components. This analysis explores the properties, manufacturing processes, performance benefits, challenges, and applications of vacuum brazed tungsten carbide wear parts in mining crushing, drawing on technical insights and industry practices.
1. Properties of Tungsten Carbide for Mining Crushing
Tungsten carbide is a composite material typically consisting of tungsten carbide grains (WC) embedded in a cobalt (Co) binder matrix, often with additives like titanium (Ti) or nickel (Ni) for specific applications. Its key properties make it ideal for mining crushing:
High Hardness: Tungsten carbide has a Rockwell Hardness (HRA) of 89+ and ranks around 9 on the Mohs scale, approaching the hardness of diamond. This allows it to withstand abrasive wear from hard materials like iron ore, copper ore, and granite.
Wear Resistance: The unique combination of hardness and toughness enables tungsten carbide to resist abrasion, erosion, and surface degradation during prolonged contact with rough materials.
Impact Resistance: Despite its hardness, the cobalt binder provides sufficient toughness to absorb high-impact forces encountered in crushing operations, preventing brittle fracture.
Corrosion Resistance: Tungsten carbide is resistant to chemical reactions and corrosion, ensuring performance in wet or chemically aggressive mining environments.
Thermal Stability: With a high melting point, tungsten carbide maintains structural integrity under elevated temperatures generated during crushing.
These properties ensure that tungsten carbide wear parts outperform traditional materials like high-manganese steel, which often fail under high-stress abrasive conditions.
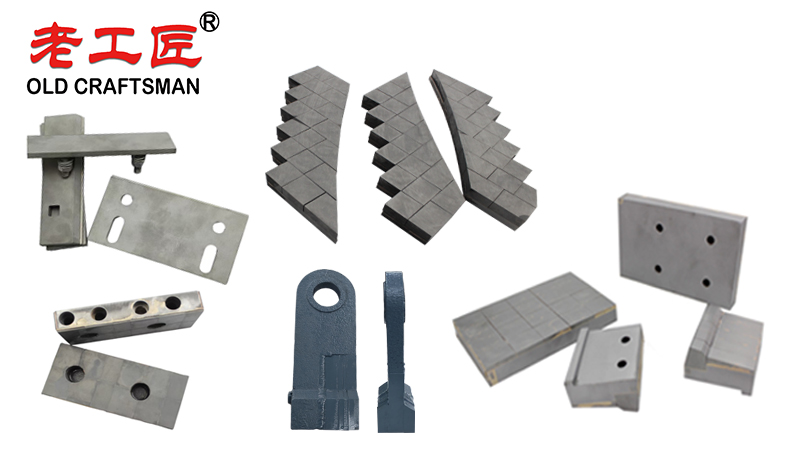
2. Vacuum Brazing Process for Tungsten Carbide Wear Parts
Vacuum brazing is a high-precision joining technique that bonds tungsten carbide to steel substrates using a filler metal (brazing alloy) in a vacuum environment. This process is favored for mining wear parts due to its ability to produce strong, reliable joints without compromising the carbide’s properties. Key aspects of the process include:
Process Overview
- Surface Preparation: Both tungsten carbide and steel surfaces must be meticulously cleaned to remove contaminants like oil, grease, oxides, or carbon residues. Common methods include sandblasting, grinding, polishing, or chemical cleaning (e.g., solvent degreasing or electrolytic etching). Clean surfaces ensure proper wetting and bonding by the brazing alloy.
- Filler Metal Selection: Common brazing alloys include:
- Copper-based alloys: Pure copper or copper-nickel-manganese alloys provide good wettability and bond strength on tungsten carbide.
- Silver-based alloys: Ag-Cu-Ti or Ag-Cu-Sn-Ti alloys are used for low-temperature brazing, achieving high shear strength (e.g., 241 MPa at 740°C).
- Nickel-based alloys: Ni-Cr-Fe-B alloys (e.g., BNi-2) are used for high-temperature applications, offering excellent mechanical properties.
- Brazing Environment: Performed in a vacuum furnace to prevent oxidation, vacuum brazing ensures a clean, flux-free joint. The vacuum environment also reduces internal stresses by minimizing gas entrapment.
- Heating and Cooling: The assembly is heated to the melting point of the filler metal (typically 700–980°C), allowing it to flow and fill the gap between the carbide and steel. Controlled cooling minimizes thermal stresses due to the coefficient of thermal expansion (CTE) mismatch between carbide and steel.
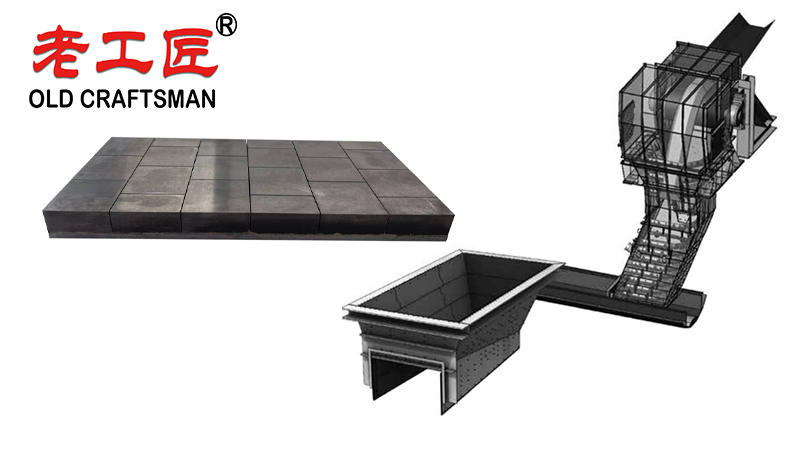
Performance Benefits in Mining Crushing
Vacuum brazed tungsten carbide wear parts offer significant advantages in mining crushing applications, directly impacting operational efficiency and cost-effectiveness:
- Extended Service Life: Tungsten carbide wear parts last 3–10 times longer than standard steel or manganese parts, reducing replacement frequency and downtime. For example, carbide crusher jaws and conveyor components maintain their shape and cutting edges over extended periods.
- Reduced Downtime: High wear resistance minimizes interruptions for maintenance, enabling continuous crushing operations.
- Cost Efficiency: Although tungsten carbide parts have a higher upfront cost, their longevity and reduced maintenance needs lead to significant long-term savings.
- Improved Safety and Reliability: Robust carbide parts withstand high-impact and abrasive conditions, reducing the risk of equipment failure and enhancing operational safety.
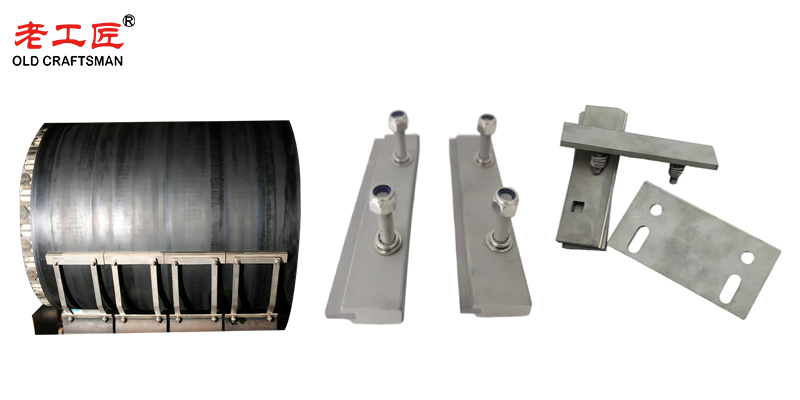
- Versatility: Vacuum brazed carbide wear parts are used in various crushing components, including:
- Crusher Jaws and Cones: Break large rocks into smaller pieces with minimal wear.
- Hammers and Grinding Rolls: Grind mined materials under high stress.
- Conveyor Components: Idlers and pulleys resist abrasion during material transport.
- Chute Liners: Protect transfer chutes in harsh environments, extending equipment life by up to 50%.
Conclusion
High-performance vacuum brazed tungsten carbide wear parts are indispensable in mining crushing due to their unmatched hardness, wear resistance, and durability. The vacuum brazing process ensures strong, reliable joints between tungsten carbide and steel, enabling wear parts to withstand the extreme conditions of mining operations. While challenges like CTE mismatch and cost persist, ongoing innovations in filler metals, brazing techniques, and quality control are addressing these issues. By reducing downtime, enhancing equipment reliability, and offering long-term cost savings, these wear parts significantly improve the efficiency and productivity of mining crushing operations.

“Zhuzhou Old Craftsman Precision Alloy Co., Ltd. could make tungsten carbide wear parts and make your equipment use life is tens of times longer than before! We specialize in providing customized carbide wear products solutions to meet the demanding requirements of industries such as aerospace, automotive, mining, and precision machining.”
Blet scarper Brazing brazingprocess CARBDIE HAMMER carbide Carbide belt scraper carbidebrazing carbide hammer Crusher CRUSHER HAMMER Informational Internal stress metal mining mold operate Refractory Brick Mold Secondary belt cleaner scraper stresses VSI VSI crusher wear plates welding work