The service life of a tungsten carbide crusher hammer depends on several critical factors, including material composition, operational conditions, and maintenance practices. Below are the key factors influencing its durability:
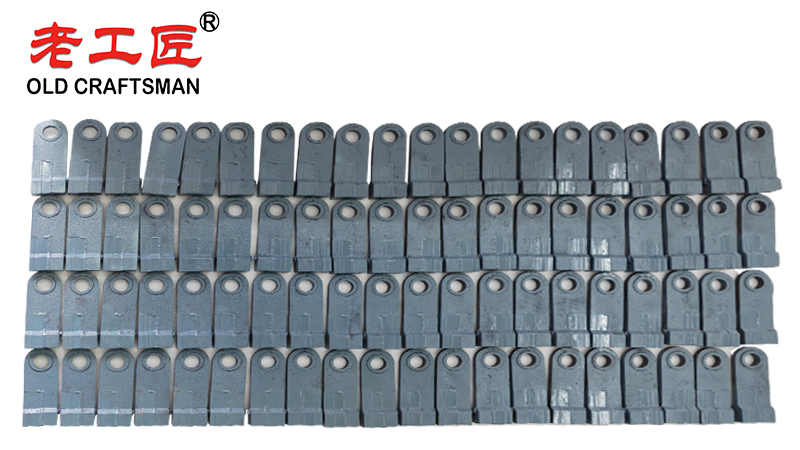
1. Tungsten Carbide Quality & Composition
- Carbide Grade: Higher-grade tungsten carbide (e.g., YG8, YG15) with a balanced cobalt (Co) binder (6-15%) offers better wear resistance and toughness.
- Grain Size: Fine-grained carbide provides higher hardness, while coarse-grained carbide improves impact resistance.
- Coating/Reinforcement: Some hammers use TiC (Titanium Carbide) or diamond coatings to enhance wear resistance further.
2. Manufacturing Process
- Sintering Quality: Properly sintered carbide ensures high density and minimal defects (voids/cracks).
- Brazing/Welding Technique: If carbide is inserted or welded onto a steel base, poor brazing can lead to detachment under impact.
- Hardfacing: Additional wear-resistant layers (e.g., Stellite or WC-Ni alloys) can extend lifespan.
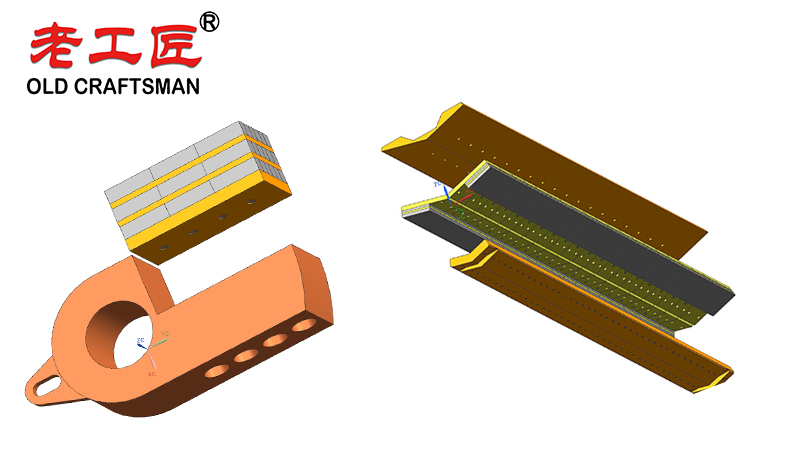
3. Feed Material Properties
- Abrasiveness: Highly abrasive materials (e.g., granite, quartz) wear down carbide faster.
- Hardness: Crushing Mohs 7+ materials (e.g., basalt, iron ore) increases wear.
- Moisture & Corrosiveness: Wet or acidic materials may cause binder corrosion (cobalt leaching).
4. Operational Conditions
- Rotor Speed & Impact Force: Excessive speed causes micro-cracks in carbide.
- Feed Size & Uniformity: Large, irregular feed leads to uneven stress distribution.
- Crushing Chamber Design: Poorly designed liners or grates cause secondary wear from rebounding material.
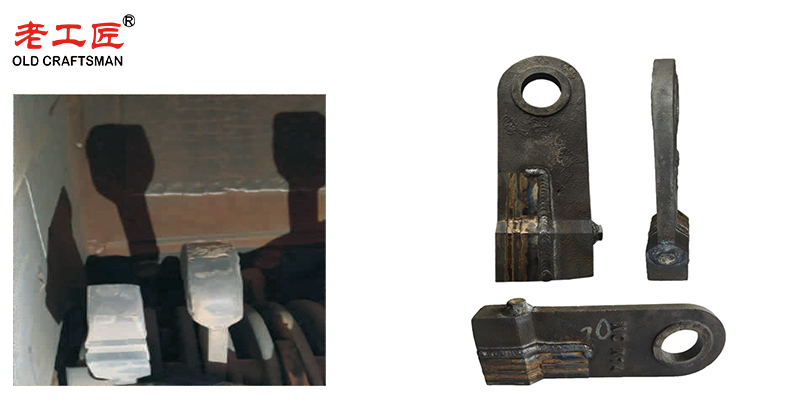
5. Mechanical & Structural Factors
- Hammer Design:
- Full Carbide Hammers: Extremely wear-resistant but brittle.
- Carbide-Tipped Hammers: Steel body with WC inserts—balances toughness and wear resistance.
- Mounting Stability: Loose hammers cause vibration-induced fractures.
6. Maintenance & Handling
- Regular Inspection: Check for cracks, chipping, or carbide loss.
- Proper Rotation/Replacement: Rotating hammers ensures even wear distribution.
- Avoid Overheating: Excessive friction (e.g., no feed) can soften the carbide.
How to Maximize Tungsten Carbide Hammer Life?
✔ Choose the right carbide grade (e.g., YG8 for moderate impact, YG15 for high impact).
✔ Optimize feed size to reduce unnecessary stress.
✔ Ensure proper brazing/welding to prevent insert detachment.
✔ Use hardfacing on steel parts to protect against secondary wear.
✔ Monitor machine vibration to avoid premature cracking.
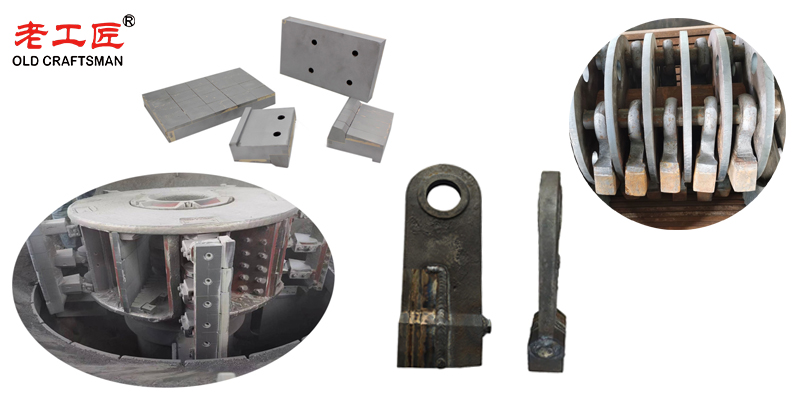
By controlling these factors, tungsten carbide crusher hammers can achieve 3-5 times longer life than standard alloy hammers in high-abrasion applications.
“Zhuzhou Old Craftsman Precision Alloy Co., Ltd. could make tungsten carbide wear parts and make your equipment use life is tens of times longer than before! We specialize in providing customized carbide wear products solutions to meet the demanding requirements of industries such as aerospace, automotive, mining, and precision machining.”
Blet scarper Brazing brazingprocess CARBDIE HAMMER carbide Carbide belt scraper carbidebrazing carbide hammer Crusher CRUSHER HAMMER Informational Internal stress metal mining mold operate Refractory Brick Mold Secondary belt cleaner scraper stresses VSI VSI crusher wear plates welding work