Tungsten carbide (WC) conveyor belt scrapers are a superior alternative to traditional steel or polyurethane scrapers, offering significant cost savings in industries like mining, cement, power plants, and bulk material handling. Here’s how they cut maintenance expenses:
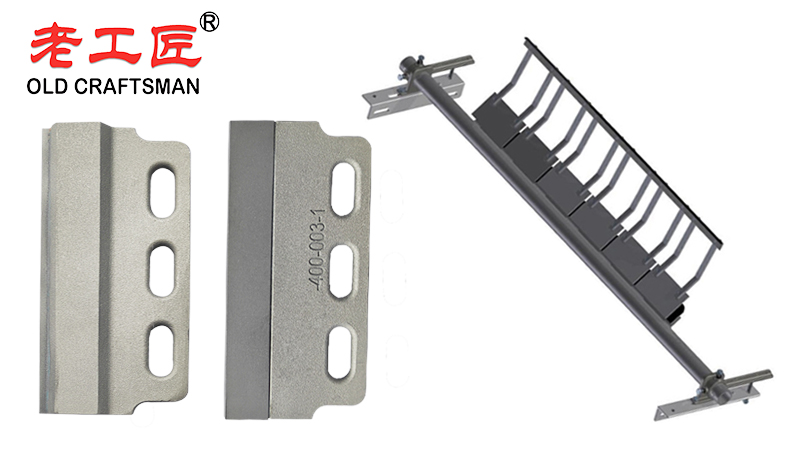
1. Extreme Wear Resistance → Fewer Replacements
- Tungsten carbide is 5-10x harder than steel and far more wear-resistant than polyurethane.
- Unlike softer scrapers that degrade quickly, carbide blades maintain sharpness longer, reducing replacement frequency.
- Result:Â Lower scraper purchase costs and less downtime for changes.
2. Prevents Belt Damage → Longer Belt Life
- Steel scrapers can gouge belts, while worn polyurethane scrapers fail to clean effectively, allowing abrasive material to accumulate.
- Carbide scrapers provide precise cleaning without damaging the belt surface.
- Result: Extends belt lifespan by 30-50%, saving thousands in premature belt replacements.
3. Better Cleaning Efficiency → Reduced Carryback
- A sharp carbide blade removes 99%+ of material carryback, preventing buildup on rollers and pulleys.
- Less residue means fewer belt misalignments, roller failures, and idler replacements.
- Result:Â Lower labor and parts costs for secondary maintenance.
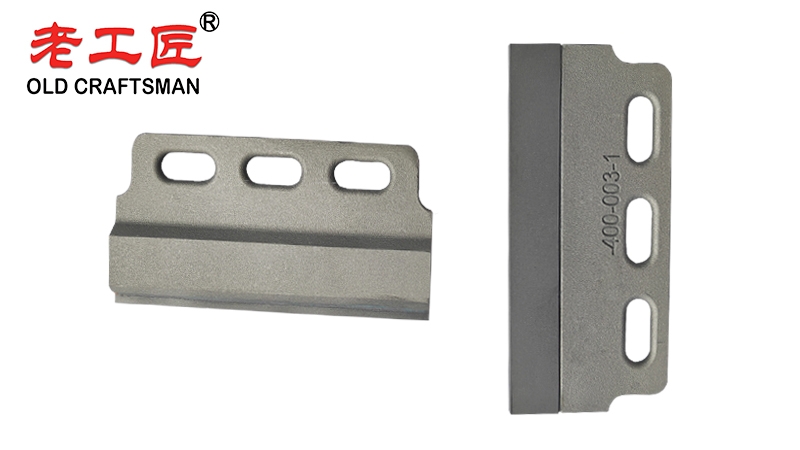
4. Reduced Downtime for Maintenance
- Fewer scraper replacements mean less frequent shutdowns for belt cleaning system overhauls.
- Carbide scrapers often last 2-5x longer than steel or polyurethane in abrasive environments.
- Result:Â Higher production uptime and lower labor costs.
5. Corrosion & High-Temperature Resistance
- Unlike steel, carbide does not rust, making it ideal for wet or chemically aggressive environments (e.g., mining, salt handling).
- Maintains hardness even at high temperatures (e.g., cement kilns, hot slag handling).
- Result:Â No performance drop in harsh conditions, reducing unexpected failures.
6. Lower Total Cost of Ownership (TCO)
- While carbide scrapers have a higher upfront cost, their durability means:
- Fewer replacements (1 carbide scraper can outlast 5+ steel scrapers).
- Less labor for installation and adjustments.
- Reduced secondary damage to belts, rollers, and pulleys.
- Result: 30-60% lower long-term costs compared to traditional scrapers.
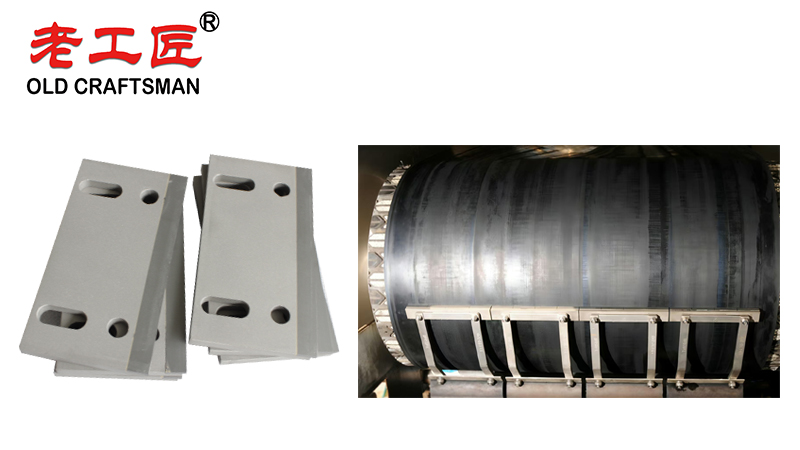
Industries That Benefit Most:
✔ Mining & Quarries – Handles abrasive ores, coal, and aggregates.
✔ Cement & Steel Plants – Resists high temperatures and clinker buildup.
✔ Power Generation – Effective for coal and biomass ash removal.
✔ Bulk Material Handling – Ideal for grains, fertilizers, and salt.
Conclusion
Tungsten carbide conveyor belt scrapers cut maintenance costs by:
✅ Lasting longer than steel or polyurethane scrapers.
✅ Protecting belts from wear and damage.
✅ Reducing carryback, preventing secondary equipment failures.
✅ Minimizing downtime for replacements and repairs.
For maximum savings, pair carbide scrapers with proper tensioning and alignment systems.
“Zhuzhou Old Craftsman Precision Alloy Co., Ltd. could make tungsten carbide wear parts and make your equipment use life is tens of times longer than before! We specialize in providing customized carbide wear products solutions to meet the demanding requirements of industries such as aerospace, automotive, mining, and precision machining.”
Blet scarper Brazing brazingprocess CARBDIE HAMMER carbide Carbide belt scraper carbidebrazing carbide hammer Crusher CRUSHER HAMMER Informational Internal stress metal mining mold operate Refractory Brick Mold Secondary belt cleaner scraper stresses VSI VSI crusher wear plates welding work