Conveyor belt scrapers have undergone significant material evolution in mining applications, transitioning from traditional steel designs to advanced tungsten carbide solutions. This shift has dramatically improved scraper performance, longevity, and cost-effectiveness in the harsh mining environment.
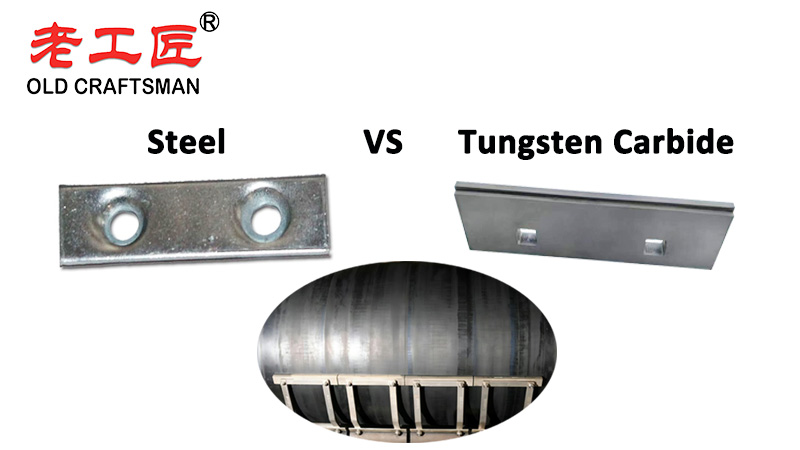
Steel Scrapers: The Traditional Approach
For decades, steel scrapers were the industry standard:
- Composition: Typically made from hardened or mild steel
- Advantages:
- Low initial cost
- Easy to manufacture and replace
- Limitations:
- Rapid wear in abrasive mining conditions
- Frequent replacement requirements
- Potential for belt damage from worn edges
- High long-term maintenance costs
The Transition to Tungsten Carbide
The mining industry’s shift to tungsten carbide scrapers addressed many steel limitations:
Why Tungsten Carbide?
- Exceptional hardness (8.5-9 on Mohs scale vs. steel’s 4-4.5)
- Superior wear resistance (3-10 times longer life than steel)
- Maintained sharp edge throughout service life
- Reduced belt wear due to consistent scraper profile
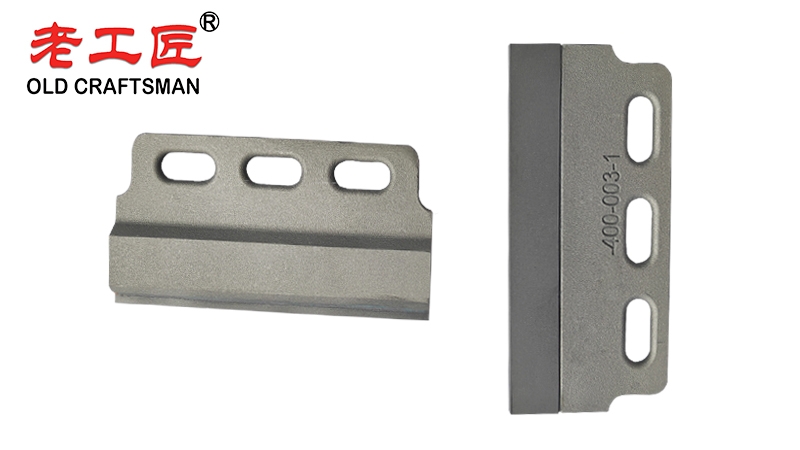
Design Innovations
Modern tungsten carbide scrapers feature:
- Carbide-tipped blades (combining carbide benefits with steel’s structural support)
- Modular designs for easy replacement of worn segments
- Adjustable tension systems for optimal blade pressure
- Multi-blade configurations for enhanced cleaning efficiency
Benefits to Mining Operations
The adoption of tungsten carbide scrapers has provided:
- Extended service intervals: Reduced downtime for maintenance
- Lower total cost of ownership: Despite higher initial cost
- Improved belt life: Cleaner operation reduces carryback and belt wear
- Enhanced safety: More reliable material containment
- Increased productivity: Consistent performance in extreme conditions
Future Developments
Emerging trends include:
- Advanced composite materials combining carbide with other alloys
- Smart scraper systems with wear monitoring sensors
- Environmentally friendly designs reducing material waste
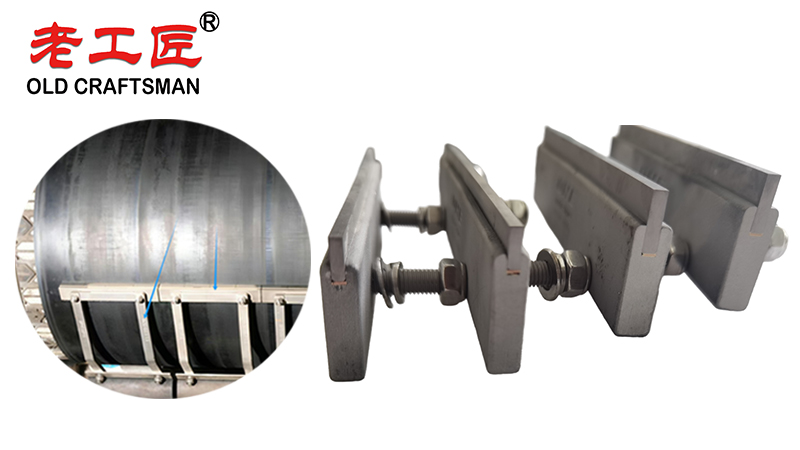
Conclusion
The evolution from steel to tungsten carbide scrapers represents a significant technological advancement in mining conveyor systems, offering improved efficiency, reliability, and cost savings in material handling operations.
By implementing these advanced tungsten carbide wear scraper solutions, mining operations can significantly improve conveyor system performance while reducing total cost of ownership through extended service life and improved operational efficiency.
“Zhuzhou Old Craftsman Precision Alloy Co., Ltd. could make tungsten carbide wear parts and make your equipment use life is tens of times longer than before! We specialize in providing customized carbide wear products solutions to meet the demanding requirements of industries such as aerospace, automotive, mining, and precision machining.”
Blet scarper Brazing brazingprocess CARBDIE HAMMER carbide Carbide belt scraper carbidebrazing carbide hammer Crusher CRUSHER HAMMER Informational Internal stress metal mining mold operate Refractory Brick Mold Secondary belt cleaner scraper stresses VSI VSI crusher wear plates welding work
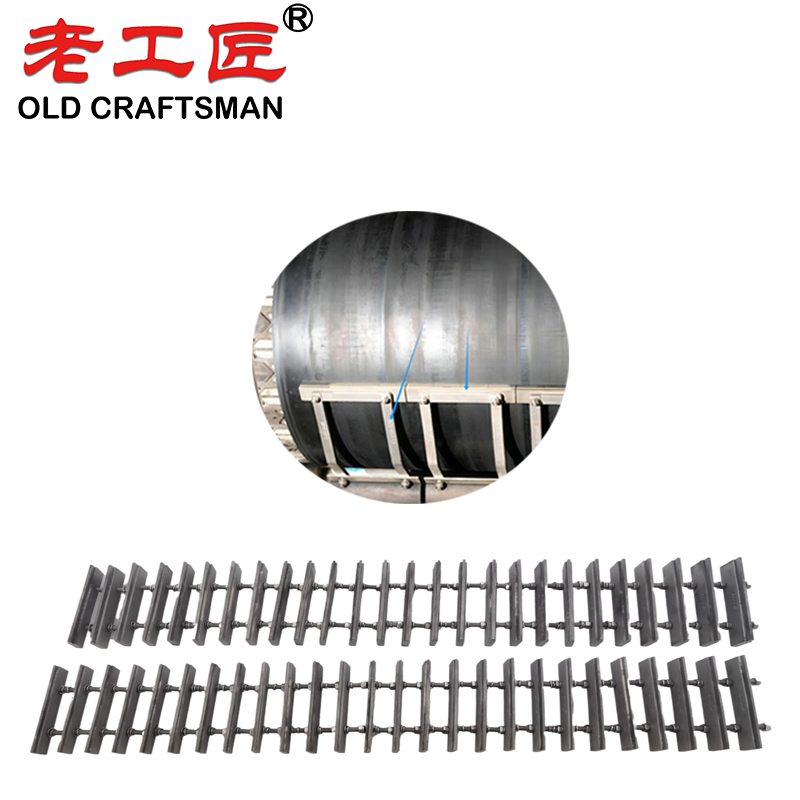