Optimizing mining processing with High-Pressure Grinding Rolls (HPGR) tungsten carbide edge blocks involves enhancing efficiency, durability, and cost-effectiveness in ore comminution. Here’s a structured approach to optimization:
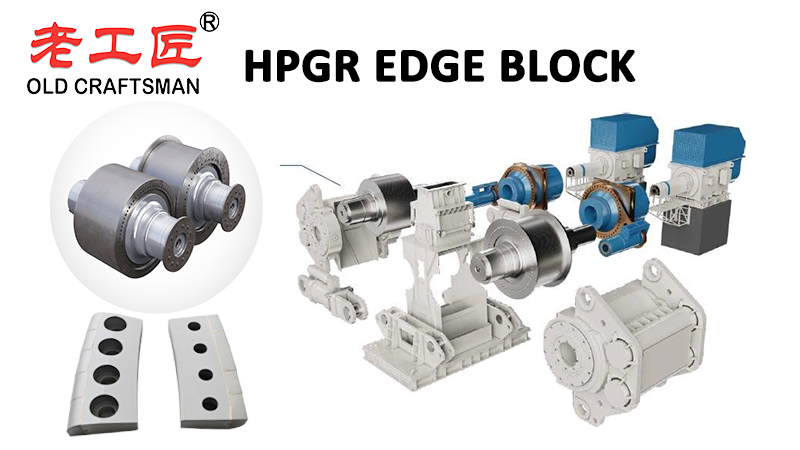
1. Benefits of Tungsten Carbide Edge Blocks in HPGR
- Superior Wear Resistance – Tungsten carbide (WC) outperforms traditional materials in abrasive environments, extending service life.
- Higher Throughput – Maintains consistent grinding gaps, improving crushing efficiency.
- Energy Efficiency – Reduces specific energy consumption compared to conventional crushing/ball milling.
- Lower Maintenance Costs – Fewer replacements due to extreme hardness (up to 1,500 HV).
2. Key Optimization Strategies
A. Material & Design Optimization
- Grade Selection: Use ultra-fine grain tungsten carbide (WC-Co) for optimal toughness and wear resistance.
- Reinforced Edges: Add diamond-enhanced coatings or functionally graded layers for high-impact zones.
- Modular Design: Replaceable edge blocks minimize downtime.
B. Operational Parameters
- Optimal Pressure Setting: Adjust based on ore hardness (typically 4–7 N/mm²).
- Feed Size Control: Pre-crush to ≤50mm to prevent uneven wear.
- Moisture Management: Keep feed moisture <5% to avoid slippage and roll wear.
C. Maintenance & Monitoring
- Predictive Maintenance: Use vibration sensors and laser scanning to detect uneven wear.
- Automated Gap Control: Real-time adjustments to maintain optimal roll gap.
- Regular Rotational Swapping: Rotate rolls to ensure even wear distribution.
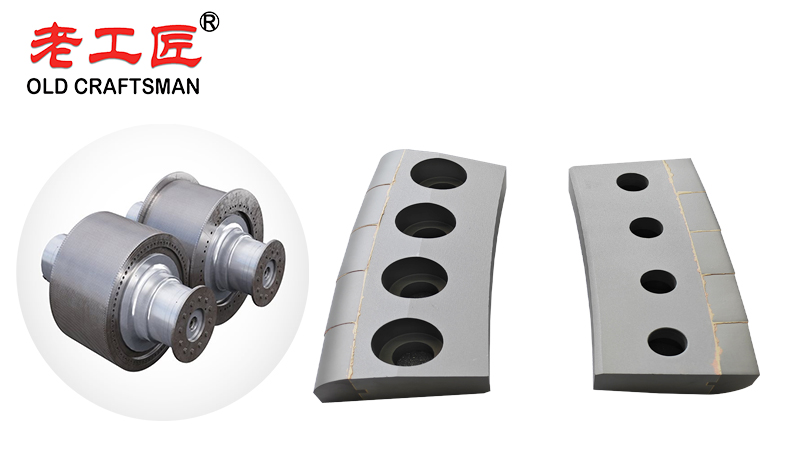
3. Case Study: Tungsten Carbide vs. Traditional Materials
Parameter | Tungsten Carbide | Alloy Steel |
---|---|---|
Lifespan | 6–12 months | 1–3 months |
Energy Savings | 20–30% reduction | Baseline |
Throughput | +15–25% | Baseline |
4. Cost-Benefit Analysis
- Higher Initial Cost (~2–3x steel) but lower TCO (Total Cost of Ownership).
- ROI Improvement: Reduced downtime + energy savings justify investment.
5. Future Trends
- Smart HPGRs: AI-driven pressure and gap optimization.
- Hybrid Composites: Nano-structured WC for even longer lifespan.
- 3D-Printed Blocks: Custom geometries for specific ore types.
Conclusion
By integrating tungsten carbide edge blocks with optimized operational practices, mining operations can achieve:
✔ Longer component life
✔ Lower energy consumption
✔ Higher throughput
✔ Reduced maintenance costs
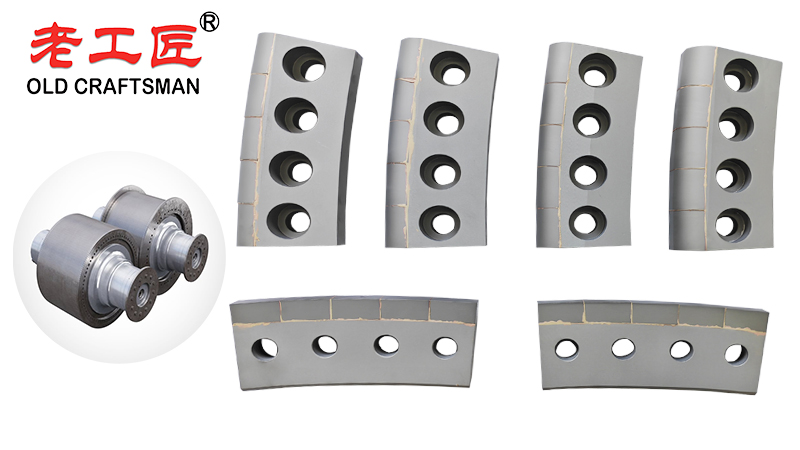
“Zhuzhou Old Craftsman Precision Alloy Co., Ltd. could make tungsten carbide wear parts and make your equipment use life is tens of times longer than before! We specialize in providing customized carbide wear products solutions to meet the demanding requirements of industries such as aerospace, automotive, mining, and precision machining.”
Blet scarper Brazing brazingprocess CARBDIE HAMMER carbide Carbide belt scraper carbidebrazing carbide hammer Crusher CRUSHER HAMMER Informational Internal stress metal mining mold operate Refractory Brick Mold Secondary belt cleaner scraper stresses VSI VSI crusher wear plates welding work