Tungsten carbide (WC) is a highly durable ceramic material widely used in industrial applications due to its extreme hardness, wear resistance, and thermal stability. It is typically combined with cobalt (Co) or nickel (Ni) binders to form cemented carbide grades. Below are common tungsten carbide grades and their applications:
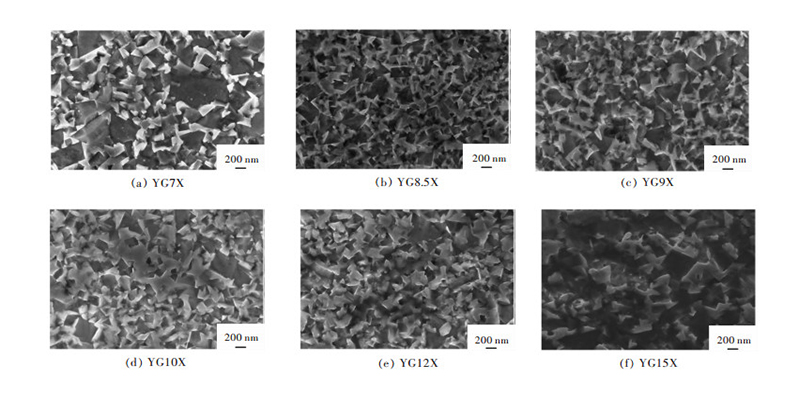
1. Common Tungsten Carbide Grades
Tungsten carbide grades are classified based on their composition, grain size, and binder content (usually cobalt or nickel). Here are the main categories:
A. Straight Grades (WC-Co)
These grades consist of tungsten carbide with cobalt as the binder. The hardness and toughness vary based on the cobalt content and grain size.
Grade | Cobalt (%) | Grain Size | Hardness (HRA) | Transverse Rupture Strength (MPa) | Key Properties |
---|---|---|---|---|---|
K10 / C2 | 3-6% | Ultra-fine | 92-94 | 2000-3500 | High hardness, wear-resistant |
K20 / C6 | 6-8% | Fine | 90-92 | 2500-4000 | Balanced hardness & toughness |
K30 / C10 | 10-12% | Medium | 88-90 | 3000-4500 | High toughness, impact-resistant |
K40 / C15 | 15-20% | Coarse | 85-88 | 3500-5000+ | Very tough, shock-resistant |
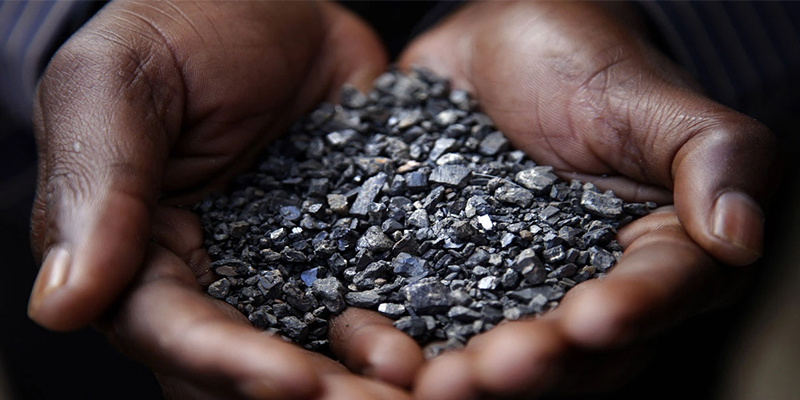
B. Micrograin Grades (Submicron & Nano WC)
- Ultra-fine grain sizes (<0.5µm) for extreme hardness and precision.
- Used in cutting tools, PCB drills, and medical instruments.
- Example: K05 (0.2-0.5µm grain, 3-6% Co, HRA 93-95).
C. Corrosion-Resistant Grades (WC-Ni or WC-Ni-Cr)
- Nickel or nickel-chromium binders instead of cobalt for chemical resistance.
- Used in marine, chemical, and food processing applications.
- Example:Â C10-Ni (10% Ni, HRA 88-90).
D. High-Temperature Grades (WC-TiC-TaC-Co)
- Added titanium carbide (TiC) and tantalum carbide (TaC) for high-temperature stability.
- Used in metal cutting inserts (e.g., P, M, K ISO classifications).
E. Wear-Resistant Grades (WC with Special Additives)
- Enhanced with chromium carbide (Cr3C2) for oxidation resistance.
- Example:Â K15X (6% Co, Cr3C2 addition, HRA 91-92).
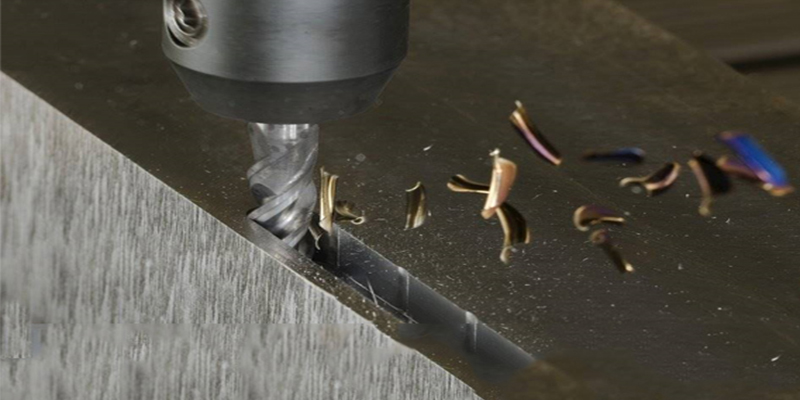
2. Applications of Tungsten Carbide Grades
Grade Type | Typical Applications |
---|---|
K10 / Ultra-Fine | Precision cutting tools, PCB drills, wear parts, engraving tools |
K20 / K30 | Milling inserts, mining tools (drill bits), punches, dies |
K40 / High-Cobalt | Heavy-duty rock drilling, oil & gas tools, stamping dies |
Micrograin | Medical tools, micro-drills, high-precision cutting |
WC-Ni (Corrosion-Resistant) | Seals, valves, marine components, chemical processing |
WC-TiC-TaC (High-Temp) | Metal cutting inserts (steel, cast iron machining) |
Cr3C2-Modified | High-temperature wear parts, furnace components |
3. Industry-Specific Uses
- Mining & Construction:Â Drill bits, road planing picks (K30-K40 grades).
- Metalworking:Â Cutting inserts (P/M/K grades), end mills (K10-K20).
- Oil & Gas:Â Downhole tools, wear rings (high-cobalt grades).
- Aerospace:Â Turbine blade coatings, wear-resistant components.
- Medical:Â Surgical blades, dental drills (ultra-fine micrograin).
- Electronics:Â PCB micro-drills (submicron WC-Co).
4. Selection Criteria
- Hardness vs. Toughness:Â Higher cobalt = more toughness but lower hardness.
- Grain Size:Â Finer grains = sharper edges but less impact resistance.
- Environment:Â Corrosive conditions require Ni-binder grades.
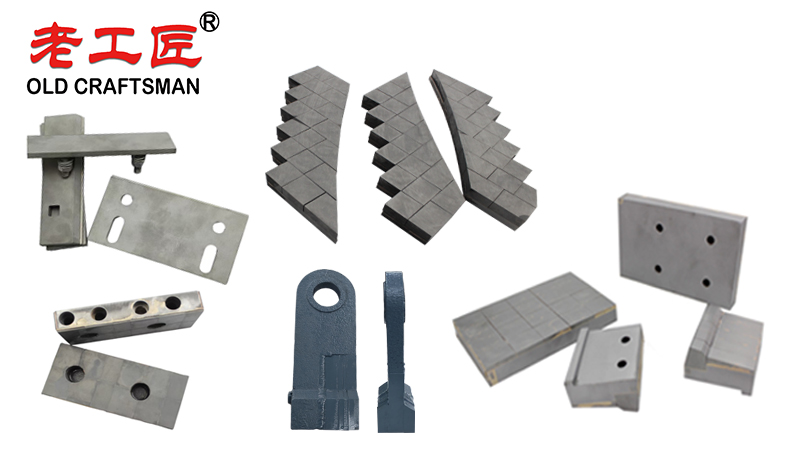
“Zhuzhou Old Craftsman Precision Alloy Co., Ltd. could make tungsten carbide wear parts and make your equipment use life is tens of times longer than before! We specialize in providing customized carbide wear products solutions to meet the demanding requirements of industries such as aerospace, automotive, mining, and precision machining.”
Blet scarper Brazing brazingprocess CARBDIE HAMMER carbide Carbide belt scraper carbidebrazing carbide hammer Crusher CRUSHER HAMMER Informational Internal stress metal mining mold operate Refractory Brick Mold Secondary belt cleaner scraper stresses VSI VSI crusher wear plates welding work