Tungsten carbide (WC) is an exceptional material choice for intensive mixer blades due to its outstanding properties, making it ideal for demanding mixing applications in industries like ceramics, powder metallurgy, chemicals, and pharmaceuticals. Below are the key benefits of using tungsten carbide for intensive mixer blades:
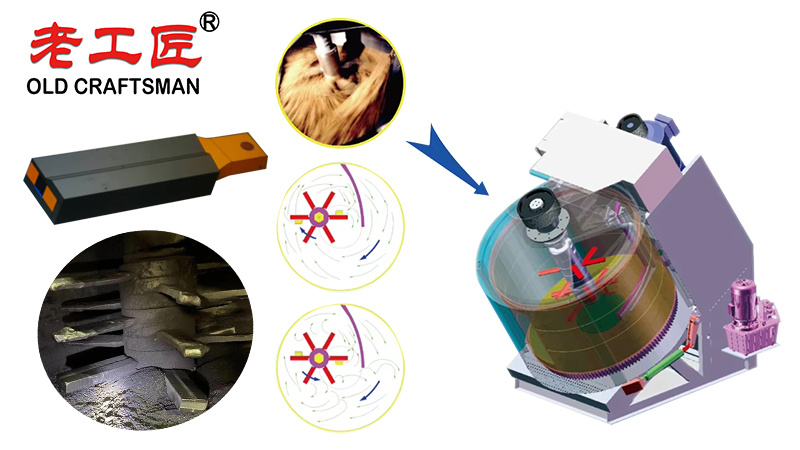
1. Exceptional Wear Resistance
- Tungsten carbide is one of the hardest materials available (HV ~1600-2000), significantly outperforming steel and even some ceramics.
- Resists abrasive wear from hard particles (e.g., ceramics, metal powders), extending blade lifespan.
- Reduces downtime and maintenance costs compared to traditional steel blades.
2. High Strength & Toughness
- Combines extreme hardness with good fracture toughness (especially in WC-Co grades).
- Withstands high mechanical stresses and impacts without chipping or cracking.
- Ideal for mixing dense or viscous materials that exert heavy loads on the blades.
3. Corrosion & Chemical Resistance
- Highly resistant to acids, alkalis, and corrosive environments (especially when using nickel-bonded WC grades).
- Suitable for mixing chemically aggressive materials (e.g., battery slurries, pharmaceuticals).
4. Heat Resistance & Stability
- Maintains hardness and structural integrity at high temperatures (up to ~500–600°C).
- Resists thermal fatigue, making it suitable for mixing processes involving heat generation.

5. Improved Mixing Efficiency & Consistency
- Sharp edges retain their profile longer, ensuring uniform mixing over extended periods.
- Reduces material buildup (anti-adhesion properties), preventing contamination.
6. Cost-Effectiveness Over Long Term
- Despite higher initial costs, WC blades last significantly longer than steel alternatives.
- Lower replacement frequency reduces operational disruptions and long-term costs.
Applications of Tungsten Carbide Mixer Blades
- Ceramics & Powder Metallurgy: Mixing hard abrasive powders like alumina, zirconia, or tungsten.
- Battery Manufacturing: Homogenizing electrode slurries (Li-ion battery production).
- Pharmaceuticals: Precise mixing of active ingredients without contamination.
- Chemical Processing: Handling corrosive or high-wear mixtures.
Considerations When Using Tungsten Carbide Blades
- Optimal Grade Selection: Cobalt-bonded WC offers toughness, while nickel-bonded grades enhance corrosion resistance.
- Design & Geometry: Precision engineering ensures optimal performance and stress distribution.
- Cost-Benefit Analysis: Justified for high-wear applications but may be overkill for less demanding mixes.
Conclusion
Tungsten carbide mixer blades provide unmatched durability, efficiency, and longevity in harsh mixing environments. While the upfront cost is higher, the reduction in maintenance, downtime, and replacement frequency makes them a superior choice for intensive mixing applications.
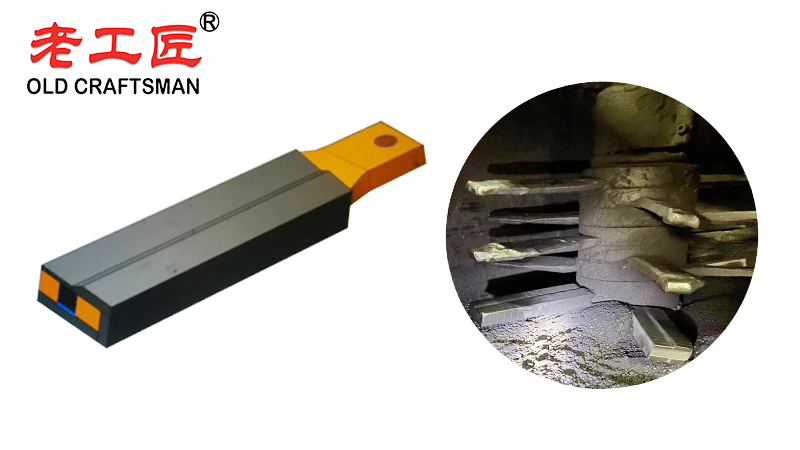
“Zhuzhou Old Craftsman Precision Alloy Co., Ltd. could make tungsten carbide wear parts and make your equipment use life is tens of times longer than before! We specialize in providing customized carbide wear products solutions to meet the demanding requirements of industries such as aerospace, automotive, mining, and precision machining.”
Blet scarper Brazing brazingprocess CARBDIE HAMMER carbide Carbide belt scraper carbidebrazing carbide hammer Crusher CRUSHER HAMMER Informational Internal stress metal mining mold operate Refractory Brick Mold Secondary belt cleaner scraper stresses VSI VSI crusher wear plates welding work