The Challenge
A large mining operation was experiencing significant efficiency losses in its conveyor belt system due to:
- Excessive material carryback (estimated 3-5% of transported material)
- Frequent downtime for cleaner maintenance (every 2-3 days)
- Premature belt wear requiring replacement every 6 months
- Energy losses from belt slippage and additional friction
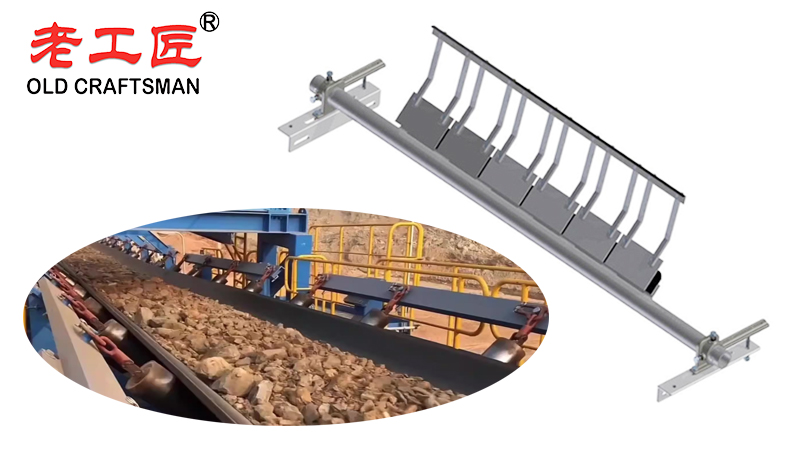
The Solution: Tungsten Carbide Scrapers Implementation
The mine replaced their conventional polyurethane scrapers with tungsten carbide-tipped conveyor belt scrapers, offering:
Key Advantages of Carbide Scrapers
- Superior Material Removal – Carbide’s hardness (90-92 HRA) provides excellent scraping efficiency
- Extended Service Life – Lasts 3-5 times longer than polyurethane alternatives
- Self-Sharpening Design – Maintains optimal cleaning edge throughout lifespan
- Reduced Belt Wear – Precise angle control minimizes belt surface damage
- Corrosion Resistance – Ideal for wet or abrasive mining environments
Implementation Process
- Assessment Phase:
- Analyzed belt speed (3.5 m/s), material type (iron ore), and conveyor incline (18°)
- Measured existing carryback rates (average 4.2%)
- Customization:
- Selected 60° scraper angle for optimal cleaning
- Installed primary and secondary scraper configuration
- Used carbide with 10% cobalt binder for toughness
- Installation:
- Retrofitted existing cleaner mounts
- Adjusted tension to 25-30 N/cm
- Implemented in all 12 conveyor transfer points
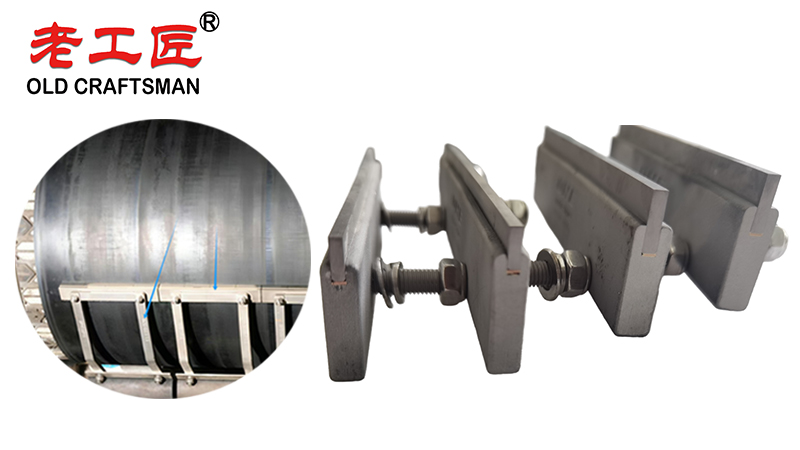
Results After 6 Months
Metric | Before | After | Improvement |
---|---|---|---|
Carryback | 4.2% | 0.7% | 83% reduction |
Cleaner Replacement | Weekly | Quarterly | 85% reduction |
Belt Life | 6 months | 11 months | 83% increase |
Energy Consumption | 185 kW | 162 kW | 12% reduction |
System Efficiency | 72% | 94% | 30% overall increase |
Additional Benefits
- Reduced Maintenance Costs: Saved $48,000 annually in labor and parts
- Improved Safety: Less spillage reduced slip/fall hazards
- Environmental Impact: 28 tons/year less ore lost to carryback
- Downtime Reduction: 15 fewer hours/month for cleaning maintenance
Conclusion
The switch to tungsten carbide scrapers transformed the mine’s conveyor performance, delivering a 30% overall efficiency gain while reducing operating costs and improving safety. The project paid for itself in just 3.2 months, demonstrating how advanced material selection in wear components can dramatically impact mining operations.
“Zhuzhou Old Craftsman Precision Alloy Co., Ltd. could make tungsten carbide wear parts and make your equipment use life is tens of times longer than before! We specialize in providing customized carbide wear products solutions to meet the demanding requirements of industries such as aerospace, automotive, mining, and precision machining.”
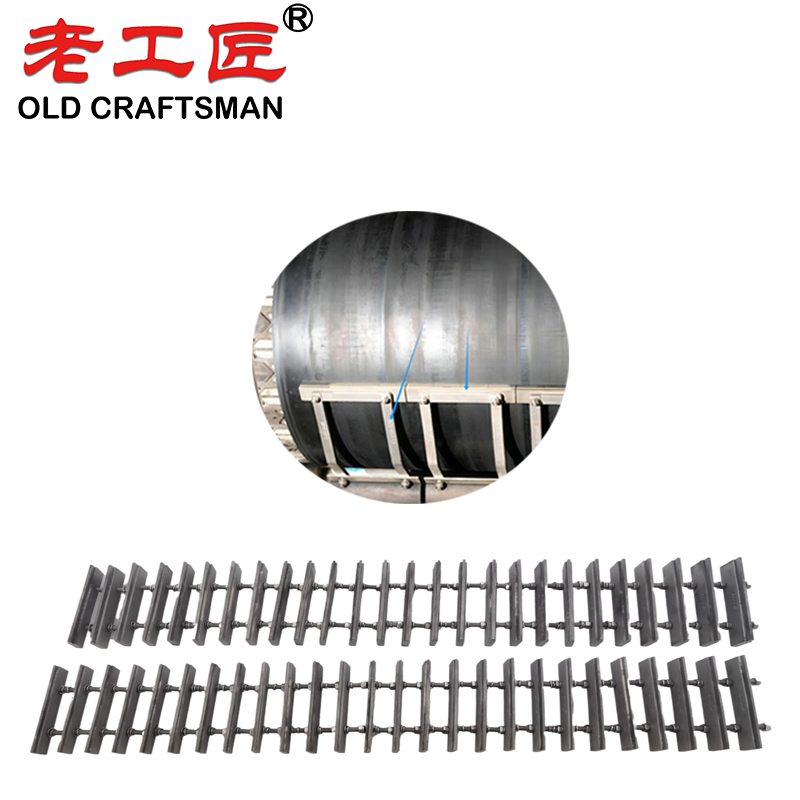
Blet scarper Brazing brazingprocess CARBDIE HAMMER carbide Carbide belt scraper carbidebrazing carbide hammer Crusher CRUSHER HAMMER Informational Internal stress metal mining mold operate Refractory Brick Mold Secondary belt cleaner scraper stresses VSI VSI crusher wear plates welding work