The Brazing or Welding Techniques of Carbide and Steel
Cemented carbide contains a relatively high content of carbides and alloy elements. Although welding can be carried out, it is prone to hardened structure and may crack during welding. Effective process measures must be taken to obtain satisfactory welded joints. At present, the commonly used welding methods for welding hard alloy and steel in production include oxygen-acetylene flame brazing, vacuum brazing, arc welding, inert gas shielded welding, friction welding, plasma arc welding, vacuum diffusion welding and electron beam welding. Cemented carbide and steel have the following characteristics when welding.
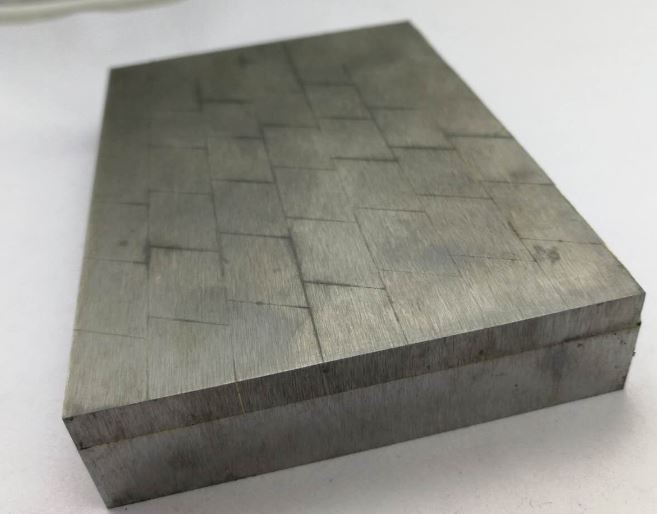
2. The relationship between hardness and crack sensitivity. The hardness of cemented carbide is directly proportional to wear resistance and welding crack sensitivity. The higher the hardness of cemented carbide, the greater the possibility of cracks during brazing. Moreover, the cemented carbide used for general finishing or super finishing is prone to cracks during brazing. According to the hardness and strength of different grades of cemented carbide, the welding crack susceptibility of cemented carbide can be judged. The order from poor to good is as follows.
YG category YG3X, YG3, YG4, YG6X, YG6, YG8, YG11, YG15
YT type YT60, YT30, YW1, YT15 (YW2), YT14, YT5
The above two types of cemented carbides, from left to right, show that the hardness and wear resistance gradually decrease, while the strength and toughness increase, and the possibility of brazing cracks decreases.
3. The influence of welding residual stress. The residual stress in the welding area is a potential hazard. Although cracks may not be found on the cemented carbide workpiece immediately after welding, it is easy to produce cracks in the subsequent sharpening, storage or use process. Cause the tool to be scrapped. When the brazing area of the cemented carbide is larger, the residual welding stress generated is greater, and the possibility of cracks is greater.
When welding cemented carbide tools, the welding residual stress must be minimized. Measures must be taken to reduce the brazing stress during welding. Measures such as lowering the brazing temperature, preheating and slow cooling before welding, selecting brazing filler metals with good plasticity, adding compensation gaskets, and improving the joint structure can be taken. When brazing a large area of cemented carbide, no matter the strength is high or low, special measures should be taken to reduce welding stress and prevent cracks.
4. Oxidation problem. When the cemented carbide is heated to above 800°C in the air, the surface of the cemented carbide begins to oxidize, forming a loose oxide layer, accompanied by decarburization. When heated to 950~1100℃, the surface layer will oxidize rapidly, and the formed oxide film will make the cemented carbide brittle and reduce the mechanical properties. The presence of surface oxide layer also reduces the strength and hardness of the weld. Taking measures during welding to minimize the oxidation of hard alloy welding parts is an important measure to improve welding quality.