Maintaining HPGR (High-Pressure Grinding Roll) tungsten carbide (WC) components is crucial for maximizing their lifespan and ensuring optimal performance. Here are key maintenance practices to extend their longevity:
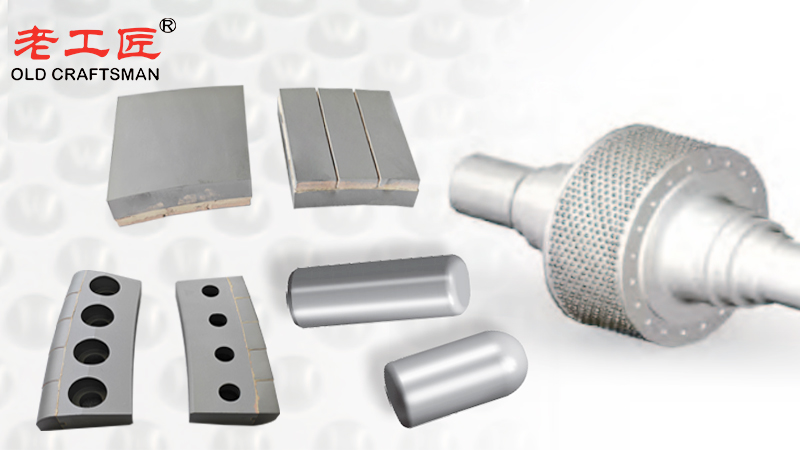
1. Proper Installation & Alignment
- Ensure correct alignment of the rolls to prevent uneven wear and premature failure.
- Follow manufacturer guidelines for torque settings and mounting procedures.
- Use proper lubrication for bearings and hydraulic systems to avoid misalignment.
2. Regular Inspection & Monitoring
- Visual Inspections:Â Check for cracks, chips, or abnormal wear patterns.
- Thickness Measurements:Â Monitor roll wear using laser scanning or calipers.
- Vibration Analysis:Â Detect misalignment or bearing issues early.
- Surface Condition Checks:Â Look for spalling, gouging, or material buildup.
3. Optimal Operating Conditions
- Avoid Overloading:Â Excessive pressure accelerates wear.
- Control Feed Size:Â Ensure feed material is within recommended size limits to prevent impact damage.
- Maintain Consistent Feed Rate:Â Fluctuations cause uneven wear.
- Monitor Moisture Content:Â Too much moisture can lead to material buildup (packing).
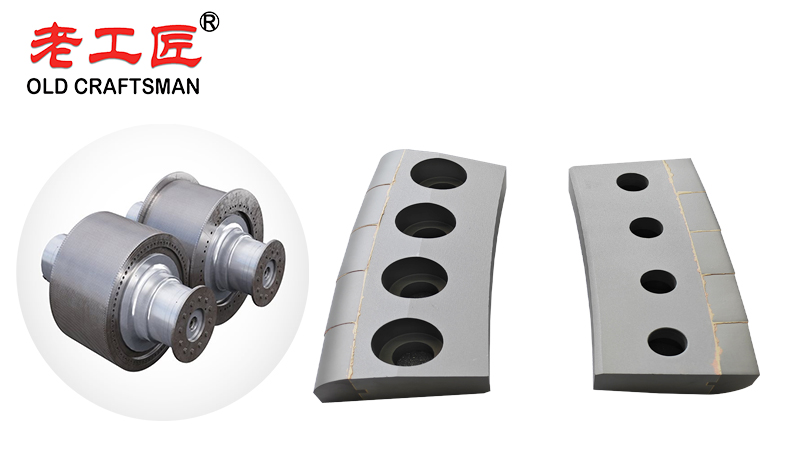
4. Effective Cleaning & Debris Management
- Remove sticky or abrasive materials that accumulate on rolls.
- Use scrapers or brushes to prevent material packing between rolls.
- Consider automated cleaning systems for continuous operation.
5. Proper Lubrication & Cooling
- Ensure bearings and hydraulic systems are well-lubricated to prevent overheating.
- Monitor roll temperature to avoid thermal stress on tungsten carbide.
6. Timely Repairs & Refurbishment
- Re-surface or recondition rolls when wear exceeds tolerance.
- Replace damaged segments instead of entire rolls (if modular).
- Use specialized welding/brazing for minor repairs (if applicable).
7. Storage & Handling Best Practices
- Store rolls in a dry, temperature-controlled environment to prevent corrosion.
- Handle with care to avoid impact damage (tungsten carbide is brittle).
- Use protective covers when not in operation.
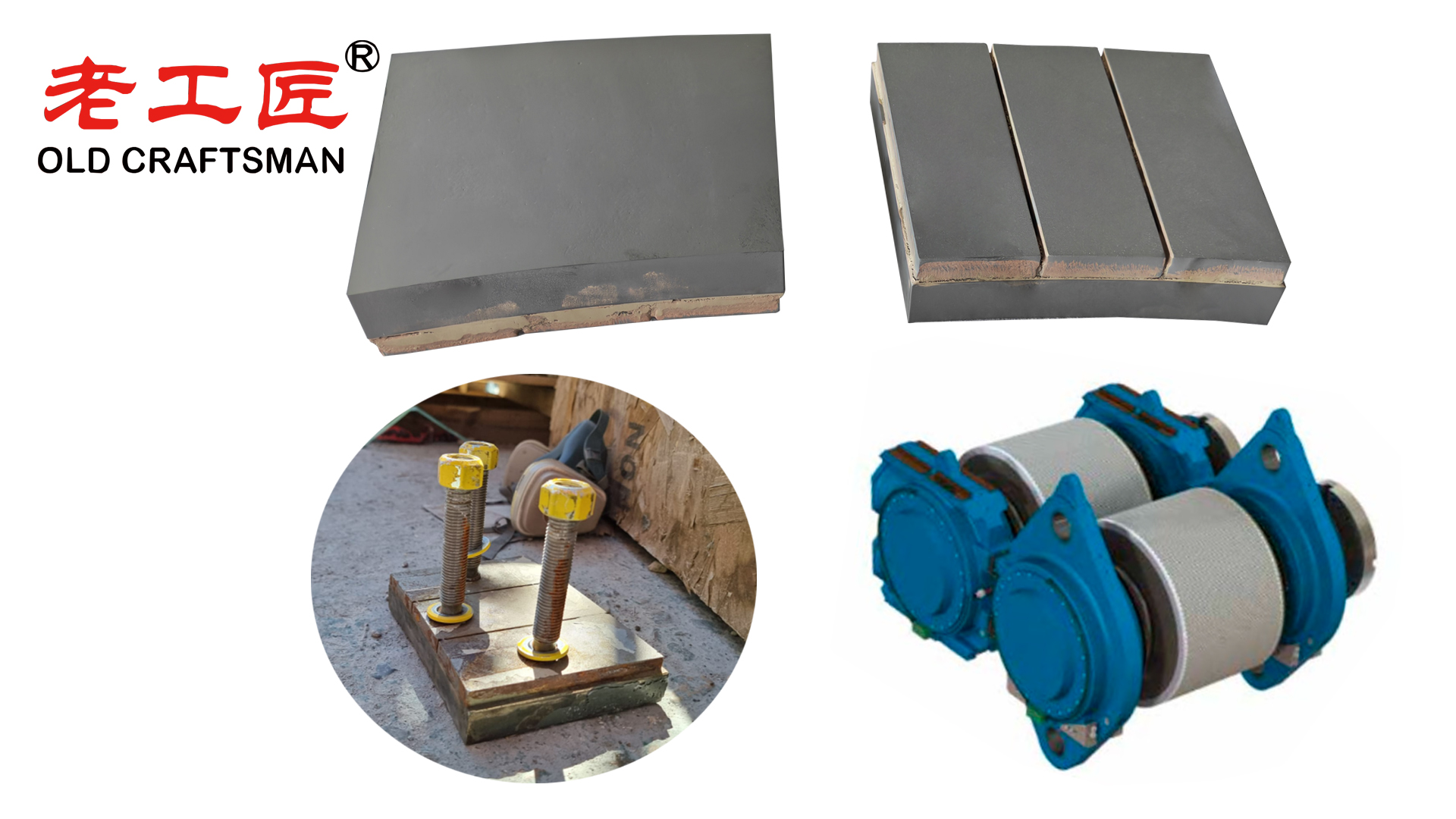
8. Operator Training & Process Optimization
- Train operators on best practices for HPGR operation.
- Optimize grinding parameters (pressure, speed, feed rate) for material type.
- Implement predictive maintenance using IoT sensors for real-time monitoring.
Conclusion
By following these maintenance practices, HPGR tungsten carbide components can achieve longer service life, reduced downtime, and lower operational costs. Regular monitoring, proper operation, and timely repairs are key to maximizing their durability.
“Zhuzhou Old Craftsman Precision Alloy Co., Ltd. could make tungsten carbide wear parts and make your equipment use life is tens of times longer than before! We specialize in providing customized carbide wear products solutions to meet the demanding requirements of industries such as aerospace, automotive, mining, and precision machining.”
Blet scarper Brazing brazingprocess CARBDIE HAMMER carbide Carbide belt scraper carbidebrazing carbide hammer Crusher CRUSHER HAMMER Informational Internal stress metal mining mold operate Refractory Brick Mold Secondary belt cleaner scraper stresses VSI VSI crusher wear plates welding work