Crushers play a critical role in cement manufacturing by reducing the size of raw materials, fuels, and clinker to optimize grinding efficiency, reduce energy consumption, and ensure product quality. Below is a detailed analysis of their applications and types in cement plants.
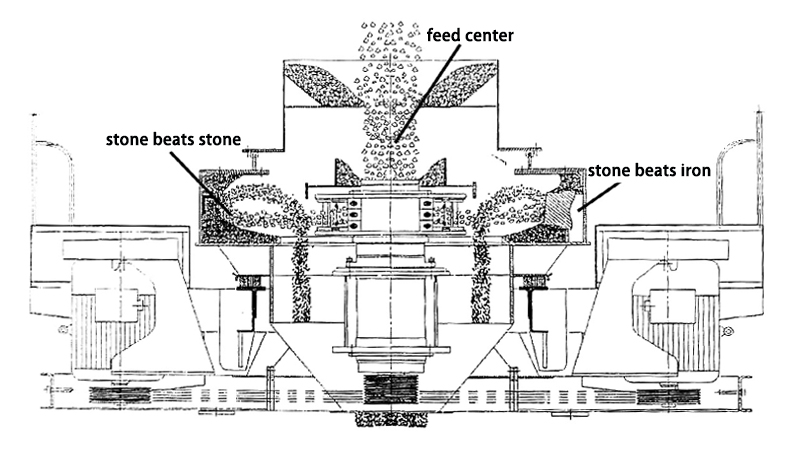
1. Key Applications of Crushers in Cement Production
(1) Raw Material Crushing (Primary & Secondary Crushing)
- Limestone, clay, iron ore, etc. must be crushed from large blocks (up to 1–1.5 m) to smaller fragments (typically <10 cm) before grinding.
- Purpose:
- Facilitates homogenization (pre-blending).
- Reduces grinding energy consumption (crushing is more efficient than grinding).
- Ensures smooth operation of raw mill feed systems.
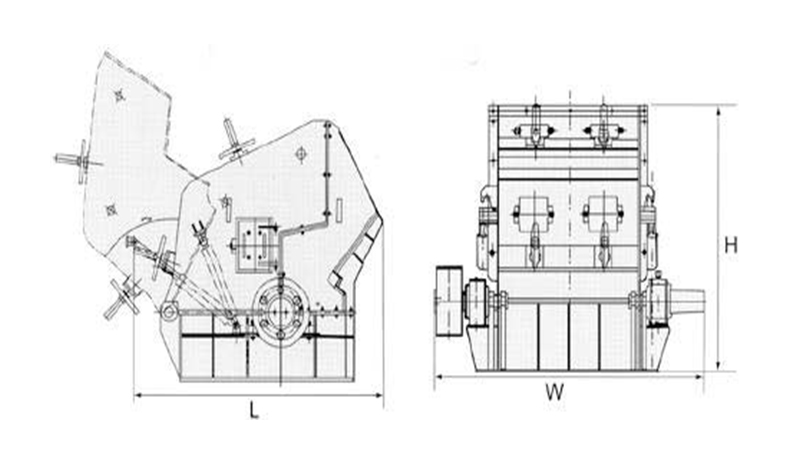
(2) Fuel (Coal/Petcoke) Crushing
- Coal is crushed to <3 cm for efficient combustion in the kiln.
- Hammer crushers or impact crushers are commonly used.
(3) Clinker Crushing (Tertiary Crushing)
- After exiting the kiln, clinker may form lumps that need further crushing (to <5 cm) before being ground into cement.
- Roll crushers or fine impact crushers are often employed.
(4) Additives (Gypsum, Slag, etc.) Crushing
- Gypsum and slag may require size reduction to improve grindability and cement setting properties.
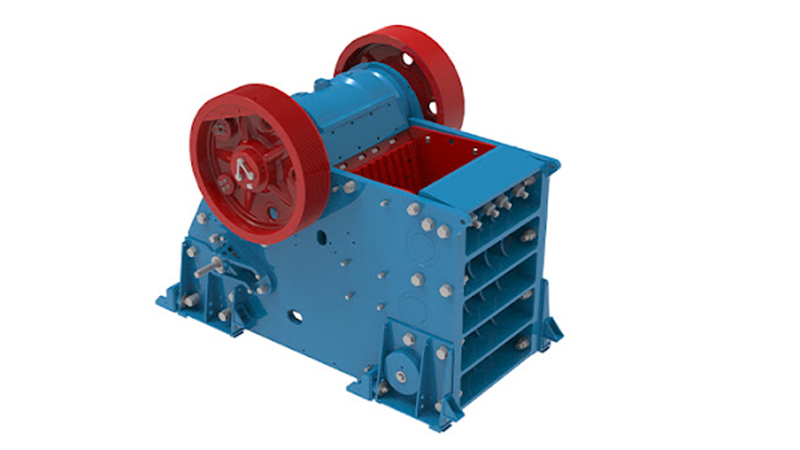
2. Types of Crushers Used in Cement Plants
Crusher Type | Application | Feed Size | Output Size | Advantages | Limitations |
---|---|---|---|---|---|
Jaw Crusher | Primary crushing (hard materials) | Up to 1.5 m | 100–300 mm | High capacity, simple structure | Limited reduction ratio |
Gyratory Crusher | Large-scale primary crushing | Up to 2 m | 150–250 mm | High throughput, low maintenance | Expensive, bulky |
Impact Crusher | Secondary crushing (medium-hard) | 300–500 mm | 20–50 mm | Good cubical shape, adjustable output | Wear-prone for abrasive materials |
Hammer Crusher | Soft & medium materials (coal, clay) | 500–800 mm | <25 mm | High reduction ratio, simple operation | High wear, not for hard materials |
Cone Crusher | Secondary/tertiary crushing | 100–300 mm | 10–50 mm | Precise control, low operating cost | Complex maintenance |
Roll Crusher | Clinker, slag, fine crushing | <50 mm | <10 mm | Low dust, energy-efficient | Low capacity, not for hard materials |
Vertical Shaft Impact (VSI) | Fine crushing (sand-like) | <50 mm | <5 mm | Excellent particle shape | High energy consumption |
3. Selection Criteria for Crushers in Cement Plants
When choosing a crusher, cement plants consider:
✔ Material Hardness (Limestone vs. clinker vs. coal)
✔ Feed & Product Size Requirements
✔ Capacity (TPH – Tons Per Hour)
✔ Energy Efficiency (Crushing vs. grinding cost)
✔ Wear Resistance & Maintenance Needs
✔ Dust & Noise Control (Environmental regulations)
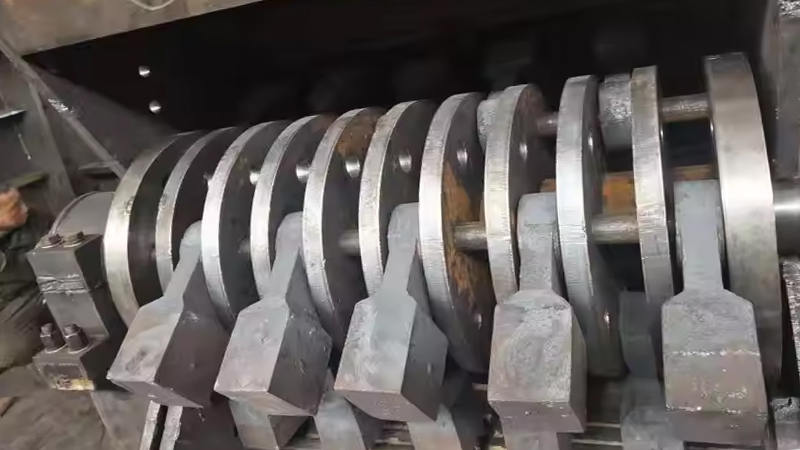
4. Trends & Innovations in Cement Plant Crushing
- Hybrid Crushers: Combining impact and compression for better efficiency.
- Mobile Crushers: Used in quarrying for flexibility.
- High-Pressure Grinding Rolls (HPGR): Pre-grinding before ball mills to save energy.
- Smart Crushers: IoT-based monitoring for predictive maintenance.
Conclusion
Crushers are indispensable in cement production, ensuring optimal material size for grinding, combustion, and final product quality. The choice of crusher depends on material properties, required output, and cost-efficiency. Modern cement plants are increasingly adopting energy-efficient and automated crushing solutions to enhance productivity and sustainability.
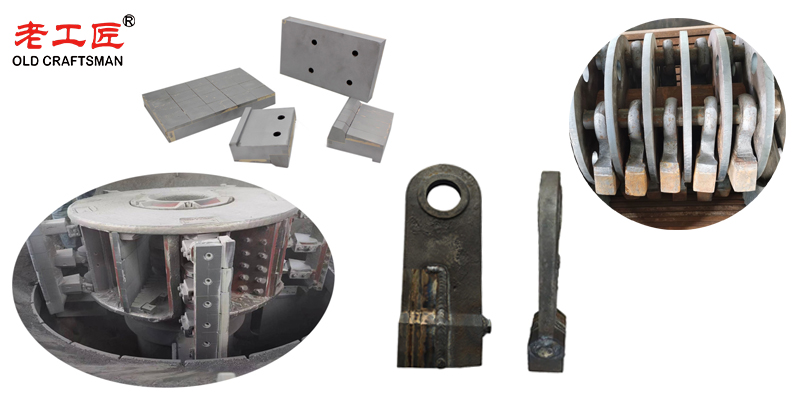
“Zhuzhou Old Craftsman Precision Alloy Co., Ltd. could make tungsten carbide wear parts and make your equipment use life is tens of times longer than before! We specialize in providing customized carbide crusher hammers solutions to meet the demanding requirements of industries such as aerospace, automotive, mining, and precision machining.”
Blet scarper Brazing brazingprocess CARBDIE HAMMER carbide Carbide belt scraper carbidebrazing carbide hammer Crusher CRUSHER HAMMER Informational Internal stress metal mining mold operate Refractory Brick Mold Secondary belt cleaner scraper stresses VSI VSI crusher wear plates welding work