Tungsten carbide (WC) wear plates are increasingly used in High-Pressure Grinding Rolls (HPGR) equipment in the mining industry due to their exceptional durability and performance in harsh operating conditions. Here are the key benefits of using tungsten carbide wear plates in HPGR applications:
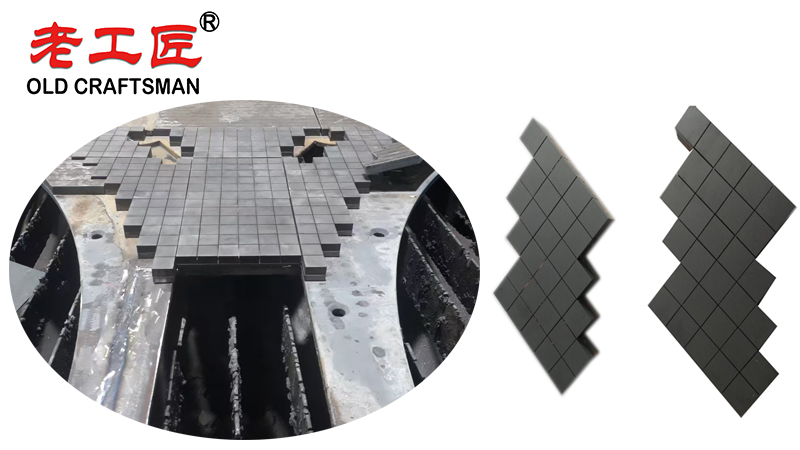
1. Exceptional Wear Resistance
- Tungsten carbide is one of the hardest materials available (HV 1500-2200), significantly outperforming steel and chromium carbide in abrasive environments.
- Reduces wear from hard minerals like quartz, iron ore, and diamonds, extending component lifespan.
2. Extended Service Life
- WC wear plates last 3-5 times longer than traditional hardened steel plates, reducing downtime for replacements.
- Minimizes maintenance frequency, lowering operational costs.
3. Improved Grinding Efficiency
- Maintains consistent roll surface profile, ensuring stable grinding performance over time.
- Reduces energy consumption by maintaining optimal pressure distribution across the rolls.
4. High Pressure & Impact Resistance
- Withstands extreme compressive forces (HPGR operates at 50-300 MPa) without cracking or spalling.
- Superior fracture toughness compared to ceramic alternatives.
5. Corrosion & Heat Resistance
- Resists oxidation and chemical degradation from slurry and moisture in wet grinding applications.
- Performs well in high-temperature conditions generated during grinding.
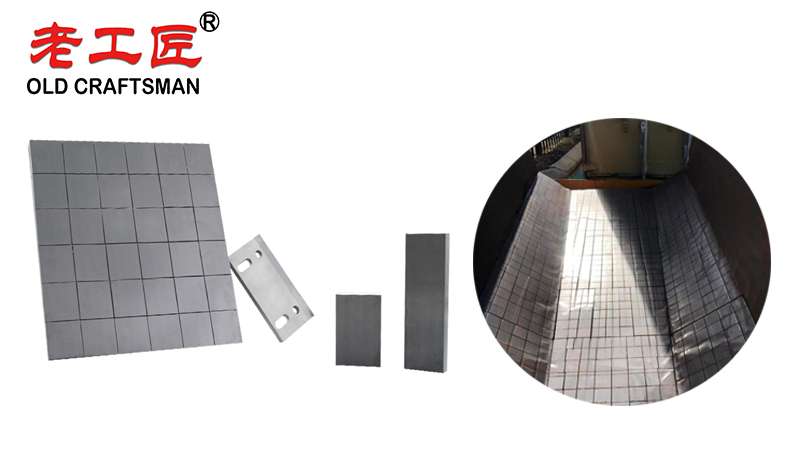
6. Cost-Effectiveness Over Time
- Despite higher initial costs, the long lifespan of WC wear plates reduces total cost of ownership (TCO).
- Fewer replacements mean less machine downtime and labor costs.
7. Customizable Solutions
- Can be manufactured in various grades (e.g., fine-grain WC for maximum wear resistance, coarse-grain for impact resistance).
- Designed as replaceable segments or full liners for easy installation.
Applications in HPGRs
- Used in roll studs, wear plates, and cheek plates to protect critical grinding surfaces.
- Ideal for processing iron ore, gold, copper, diamond, and limestone.
Conclusion
Tungsten carbide wear plates enhance HPGR performance by providing unmatched wear resistance, durability, and operational efficiency. Their adoption leads to lower maintenance costs, longer equipment life, and sustained grinding productivity, making them a superior choice for modern mining operations.
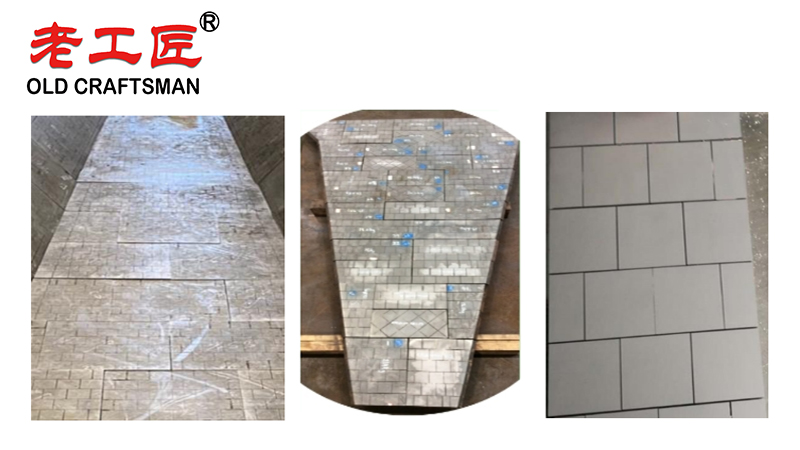
Need help choosing the HPGRt wear plate for your application? Consult Zhuzhou Old Craftsman Precision Alloy Co., Ltd. to optimize your mining equipment’s lifespan and efficiency.
“Zhuzhou Old Craftsman Precision Alloy Co., Ltd. could make tungsten carbide wear parts and make your equipment use life is tens of times longer than before! We specialize in providing customized carbide wear products solutions to meet the demanding requirements of industries such as aerospace, automotive, mining, and precision machining.”
Blet scarper Brazing brazingprocess CARBDIE HAMMER carbide Carbide belt scraper carbidebrazing carbide hammer Crusher CRUSHER HAMMER Informational Internal stress metal mining mold operate Refractory Brick Mold Secondary belt cleaner scraper stresses VSI VSI crusher wear plates welding work