Tungsten carbide wear plates are essential components in the mining industry, offering superior resistance to abrasion, impact, and corrosion. These plates extend the lifespan of mining equipment, reduce downtime, and improve operational efficiency. This guide explores their benefits, applications, and selection criteria for mining operations.
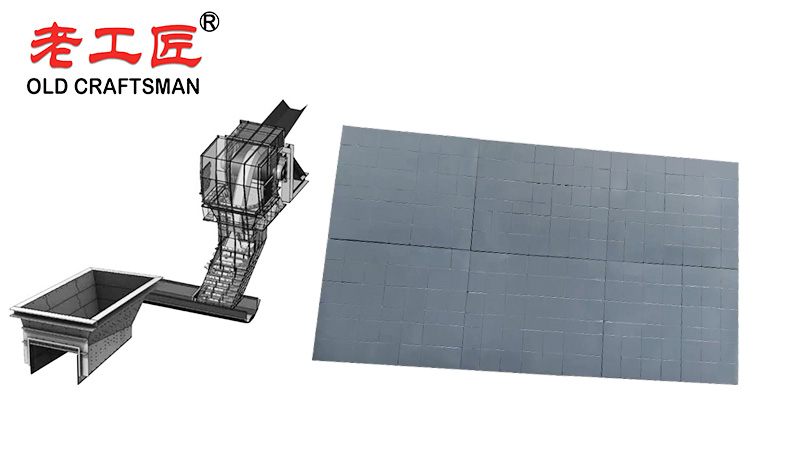
What Are Tungsten Carbide Wear Plates?
Tungsten carbide (WC) wear plates are composite materials made by embedding tungsten carbide particles in a tough, wear-resistant matrix (often a steel or binder alloy). The result is an ultra-durable material that withstands extreme mining conditions.
Key Properties:
- Extreme Hardness (Up to 90 HRA) – Resists abrasive wear from rocks, ores, and slurries.
- High Impact Resistance – Maintains structural integrity under heavy loads.
- Corrosion Resistance – Performs well in wet and chemically aggressive environments.
- Heat Resistance – Retains strength at high temperatures.
Applications in Mining
Tungsten carbide wear plates are used in:
- Excavation Equipment – Bucket liners, bulldozer blades, and shovel teeth.
- Ore Processing – Chutes, hoppers, and crusher liners.
- Conveyor Systems – Impact beds and skirting to reduce wear.
- Drilling Tools – Bit protectors and stabilizers.
- Slurry Handling – Pump housings and pipeline liners.
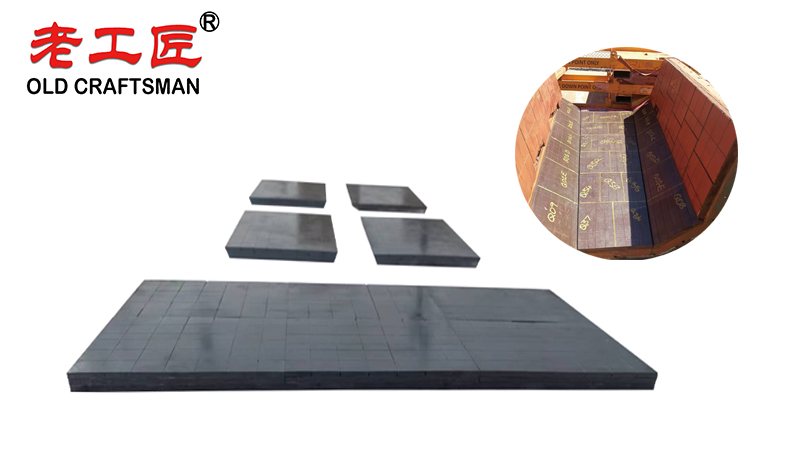
Benefits of Tungsten Carbide Wear Plates
✔ Extended Equipment Life – Lasts up to 10x longer than standard steel plates.
✔ Reduced Maintenance Costs – Fewer replacements and downtime.
✔ Improved Efficiency – Smoother material flow with less friction.
✔ Versatility – Customizable shapes and thicknesses for different mining needs.
Choosing the Right Tungsten Carbide Wear Plate
Consider these factors when selecting a wear plate:
1. Abrasion Resistance
- Higher carbide content (85-95%) for extreme abrasion.
- Lower binder content for better wear resistance but slightly reduced toughness.
2. Impact Resistance
- A balanced carbide-binder ratio (e.g., 70-80% carbide) for high-impact applications.
3. Operating Environment
- Corrosion-resistant binders (e.g., nickel-chromium) for wet or acidic conditions.
4. Plate Thickness & Attachment Method
- Thickness: 5mm to 50mm, depending on wear severity.
- Attachment: Welded, bolted, or bonded to equipment.
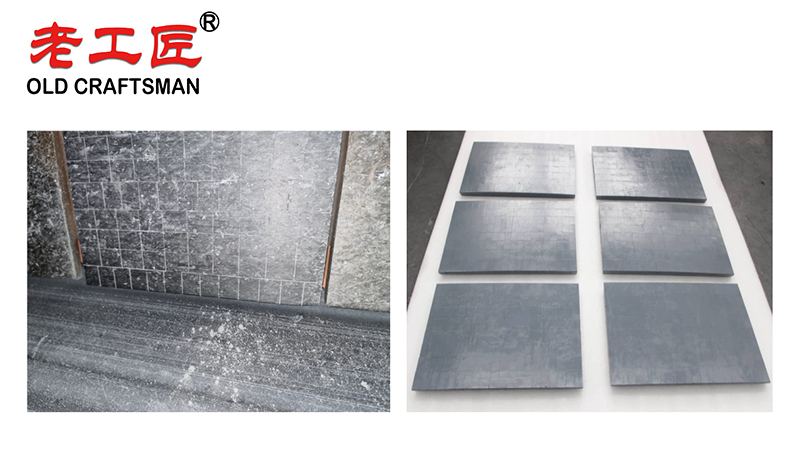
Installation & Maintenance Tips
- Proper Surface Preparation – Ensure clean, debris-free surfaces before installation.
- Correct Welding Techniques – Use low-heat methods to prevent cracking.
- Regular Inspections – Check for wear patterns and replace before failure occurs.
Tungsten Carbide vs. Alternatives
Material | Wear Resistance | Impact Resistance | Cost Efficiency | Best For |
---|---|---|---|---|
Tungsten Carbide | ⭐⭐⭐⭐⭐ | ⭐⭐⭐⭐ | High | Extreme abrasion |
Hardened Steel | ⭐⭐⭐ | ⭐⭐⭐⭐ | Medium | Moderate wear |
Ceramic Liners | ⭐⭐⭐⭐ | ⭐⭐ | Medium-High | Light impact, high abrasion |
UHMW Polyethylene | ⭐⭐ | ⭐⭐⭐ | Low | Light-duty, corrosion-prone areas |
Conclusion
Tungsten carbide wear plates are a game-changer for mining operations, offering unmatched durability and cost savings. By selecting the right grade and maintaining them properly, mining companies can significantly enhance equipment performance and reduce operational costs.
Need help choosing the best wear plate for your application? Consult Zhuzhou Old Craftsman Precision Alloy Co., Ltd. to optimize your mining equipment’s lifespan and efficiency.

“Zhuzhou Old Craftsman Precision Alloy Co., Ltd. could make tungsten carbide wear parts and make your equipment use life is tens of times longer than before! We specialize in providing customized carbide wear products solutions to meet the demanding requirements of industries such as aerospace, automotive, mining, and precision machining.”
Blet scarper Brazing brazingprocess CARBDIE HAMMER carbide Carbide belt scraper carbidebrazing carbide hammer Crusher CRUSHER HAMMER Informational Internal stress metal mining mold operate Refractory Brick Mold Secondary belt cleaner scraper stresses VSI VSI crusher wear plates welding work