Refractory brick molds are crucial in shaping high-temperature-resistant bricks used in furnaces, kilns, and industrial linings. The choice between tungsten carbide (WC) molds and common molds (typically made of alloy steel, cast iron, or hardened tool steel) depends on production needs, material abrasiveness, and cost considerations. Below is a detailed comparison:
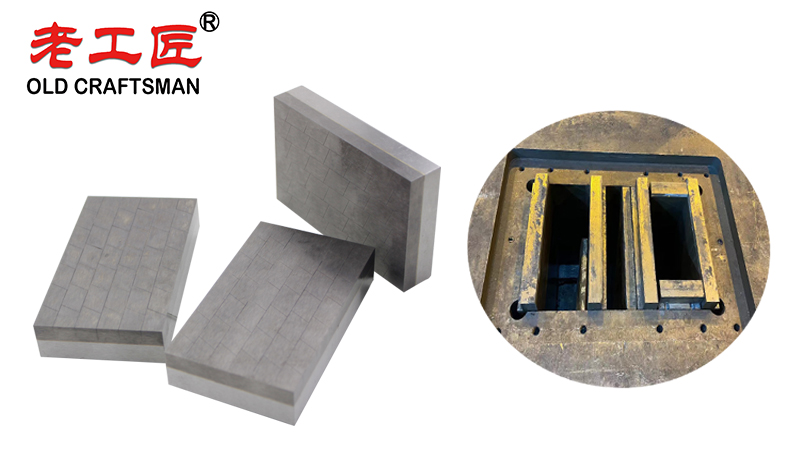
1. Material Properties
Property | Tungsten Carbide (WC) Mold | Common Mold (Steel/Cast Iron) |
---|---|---|
Hardness | Extremely high (HV 1600-2000) | Moderate (HV 500-800) |
Wear Resistance | Excellent (5-10x longer life) | Poor (requires frequent replacement) |
Compressive Strength | Very high (resists deformation) | Moderate (may deform under high pressure) |
Thermal Stability | Stable up to 600°C+ | Softens at high temperatures (~300-400°C) |
Corrosion Resistance | Highly resistant to chemicals/oxidation | Prone to rust and chemical wear |
Thermal Fatigue Resistance | Excellent (handles repeated heating/cooling) | May crack or warp over time |
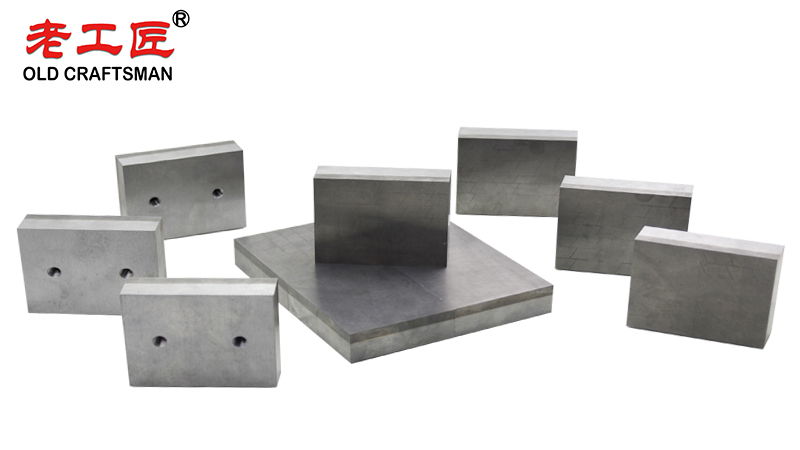
2. Performance in Refractory Brick Production
Factor | Tungsten Carbide Mold | Common Mold |
---|---|---|
Lifespan | 50,000–100,000+ cycles | 5,000–20,000 cycles |
Precision & Consistency | Maintains tight tolerances for longer | Dimensional accuracy degrades faster |
Surface Finish | Smooth, reduces sticking | Rougher, may need lubricants |
Suitability for Abrasive Materials | Best for alumina, zirconia, SiC | Wears quickly with hard materials |
High-Pressure Molding | Handles extreme pressures | May deform under high loads |
3. Cost Considerations
Aspect | Tungsten Carbide Mold | Common Mold |
---|---|---|
Initial Cost | Very high (5-10x steel) | Low to moderate |
Maintenance Cost | Minimal (rare replacement) | High (frequent repairs/replacement) |
Downtime Impact | Low (long intervals between changes) | High (frequent mold changes slow production) |
Cost per Brick | Lower in long-term production | Higher due to frequent replacements |
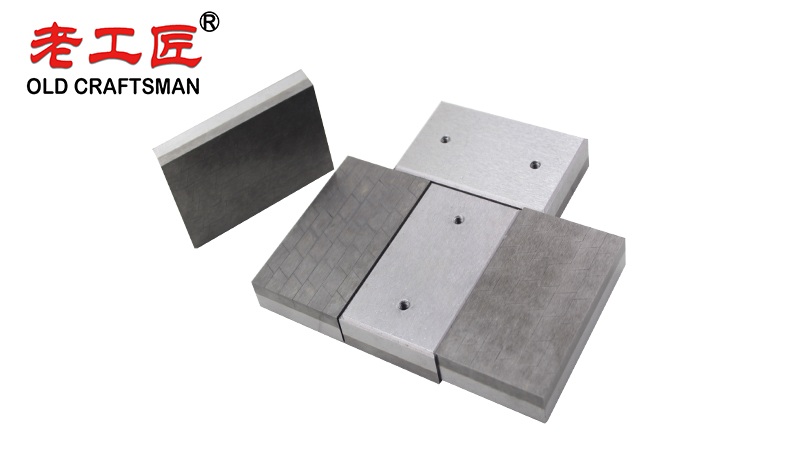
4. Best Applications
- Tungsten Carbide Molds Are Best For:
- High-volume refractory brick production.
- Abrasive materials (alumina, silicon carbide, zirconia bricks).
- High-pressure molding (hydraulic/isostatic pressing).
- Precision bricks requiring tight tolerances.
- Common Molds Are Suitable For:
- Low-to-medium production volumes.
- Less abrasive materials (fireclay, basic refractories).
- Short-run or prototype production where cost is critical.
5. Conclusion: Which One to Choose?
Choose Tungsten Carbide If: | Choose Common Mold If: |
---|---|
✔ High abrasion resistance needed | ✔ Budget is limited |
✔ Long production runs | ✔ Low-to-medium production volume |
✔ Extreme pressure/heat conditions | ✔ Non-abrasive refractory materials |
✔ Lower cost per brick in long term | ✔ Short-term or prototype needs |
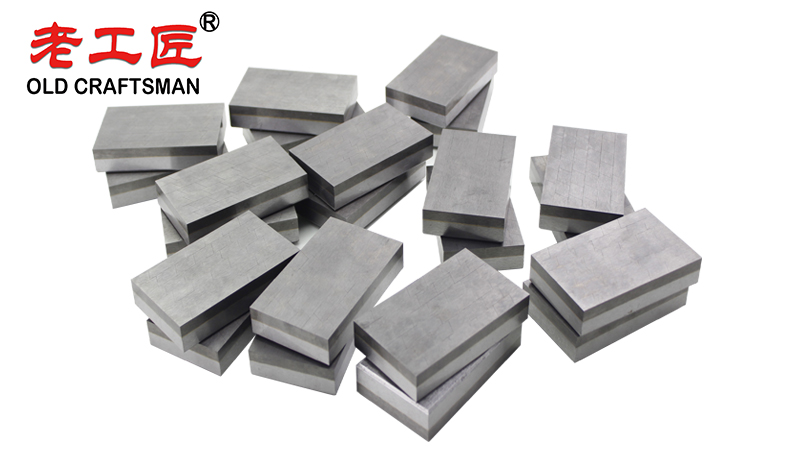
Final Verdict:
- WC molds are superior in durability, precision, and efficiency but come at a high initial cost.
- Common molds are cheaper upfront but cost more over time due to frequent replacements.
For large-scale, high-abrasion refractory production, tungsten carbide molds are the best investment. For small-scale or less demanding applications, steel or cast iron molds may suffice.
“Zhuzhou Old Craftsman Precision Alloy Co., Ltd. could make tungsten carbide wear parts and make your equipment use life is tens of times longer than before! We specialize in providing customized carbide wear products solutions to meet the demanding requirements of industries such as aerospace, automotive, mining, and precision machining.”
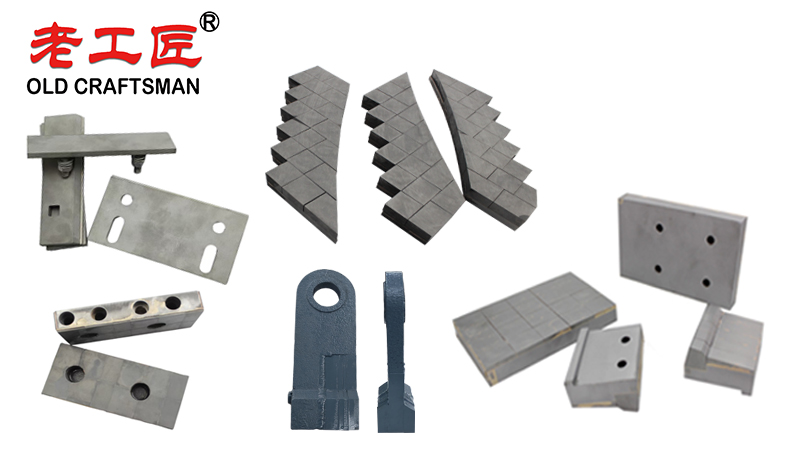
Blet scarper Brazing brazingprocess CARBDIE HAMMER carbide Carbide belt scraper carbidebrazing carbide hammer Crusher CRUSHER HAMMER Informational Internal stress metal mining mold operate Refractory Brick Mold Secondary belt cleaner scraper stresses VSI VSI crusher wear plates welding work