Mining equipment uses tungsten carbide wear-resistant parts because of their exceptional hardness, strength, and durability. Tungsten carbide, a composite material made of tungsten and carbon, has a hardness close to that of diamond, making it highly resistant to abrasion, erosion, and impact. In the harsh conditions of mining—where equipment is exposed to constant friction, high pressures, and abrasive materials like rock, ore, and sand—tungsten carbide parts significantly outlast traditional materials like steel. Here are the key reasons:
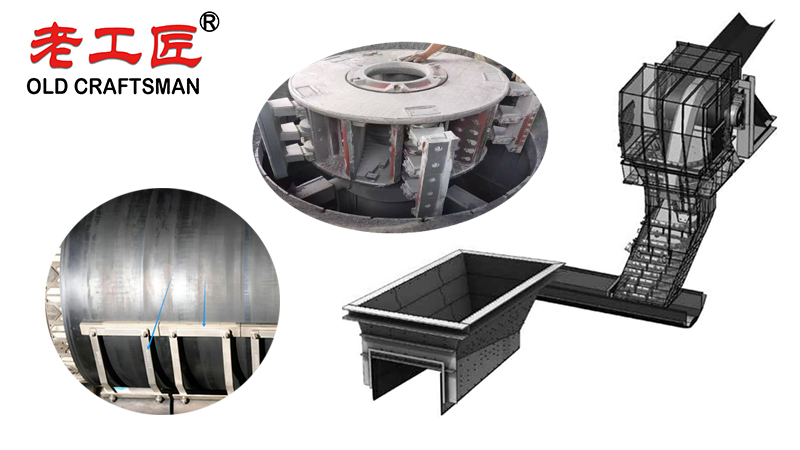
1. Extreme Hardness & Wear Resistance
- Tungsten carbide has a Mohs hardness of 9-9.5 (close to diamond at 10), making it highly resistant to abrasion from rocks, ores, and other abrasive materials.
- It significantly outperforms steel in wear life, reducing downtime and replacement costs.
2. High Compressive Strength
- WC can withstand extreme pressures, making it ideal for crushing, drilling, and cutting applications where heavy loads are involved (e.g., drill bits, crusher liners).
3. Impact Resistance (When Combined with Cobalt Binder)
- While pure tungsten carbide is brittle, when bonded with cobalt (Co) or nickel (Ni), it gains toughness, allowing it to endure repeated impacts without cracking (e.g., in mining picks, hammer tips).
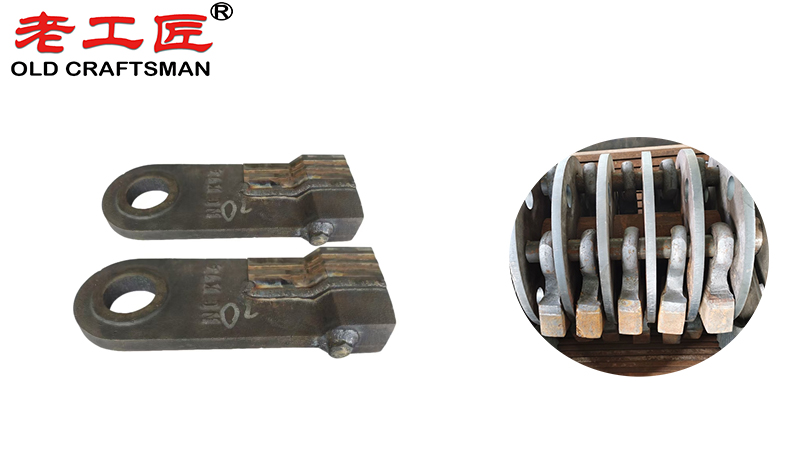
4. Corrosion & Heat Resistance
- Resists chemical corrosion from slurry, water, and acidic/alkaline conditions in mining operations.
- Maintains strength at high temperatures (up to ~500–600°C), crucial for drilling and cutting tools.
5. Cost-Effectiveness Over Time
- Though initial costs are higher than steel, tungsten carbide parts last 5–10 times longer, reducing maintenance and replacement frequency.
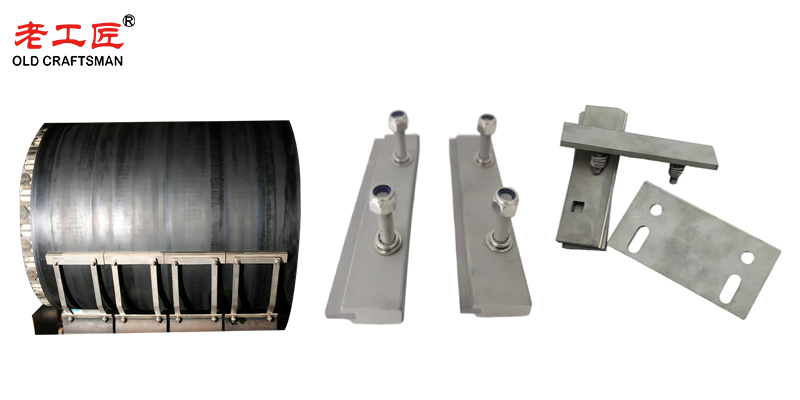
Common Mining Applications:
- Drill bits (for rock drilling)
- Crusher liners & hammers (for ore processing)
- Wear plates & nozzles (in slurry transport)
- Road planer teeth (for surface mining)
Comparison to Alternatives:
- Steel: Cheaper but wears out faster.
- Ceramics: Hard but brittle; less impact-resistant.
- Polymer composites: Lighter but unsuitable for heavy abrasion.
Conclusion:
Tungsten carbide provides the optimal balance of hardness, toughness, and longevity for mining equipment, ensuring efficiency and cost savings in highly abrasive conditions.
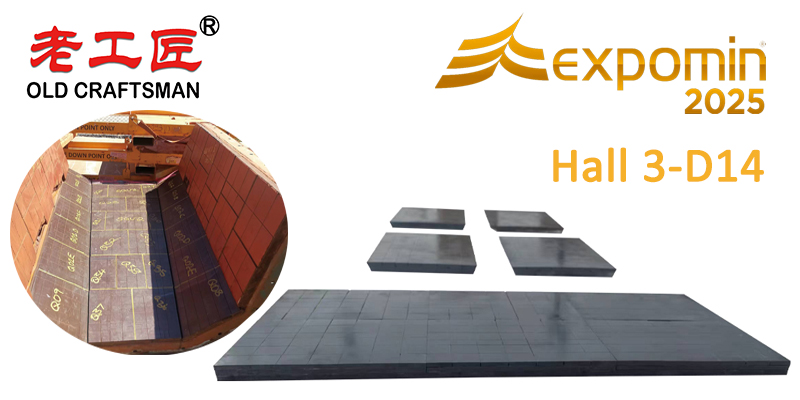
Looking Forward to EXPOMIN 2025
EXPOMIN 2025 is a fantastic opportunity for us to connect with the mining community, share our expertise, and explore new partnerships. We are particularly excited to engage with clients and partners in Chile, a country at the forefront of the global mining industry. Join us in Santiago to discover how ZZ OLD CRAFTSMAN can help you achieve greater efficiency, sustainability, and profitability in your mining operations.
Stay tuned for more updates as we prepare for EXPOMIN 2025. Follow us on ZZ OLD CRAFTSMAN Social Media Links, for the latest news and insights from our team. We can’t wait to see you in Santiago!
Blet scarper Brazing brazingprocess CARBDIE HAMMER carbide Carbide belt scraper carbidebrazing carbide hammer Crusher CRUSHER HAMMER Informational Internal stress metal mining mold operate Refractory Brick Mold Secondary belt cleaner scraper stresses VSI VSI crusher wear plates welding work