Mining conveyor belt systems often require tungsten carbide secondary scrapers for several critical reasons related to efficiency, belt longevity, and cost-effectiveness. Here’s why they are essential:
1. Enhanced Belt Cleaning Efficiency
- Primary scrapers remove most bulk material, but secondary scrapers (often tungsten carbide-tipped) ensure residual fines and sticky materials are thoroughly cleaned.
- Tungsten carbide’s hardness (HV 1500-1800) allows it to scrape off stubborn residues without damaging the belt.
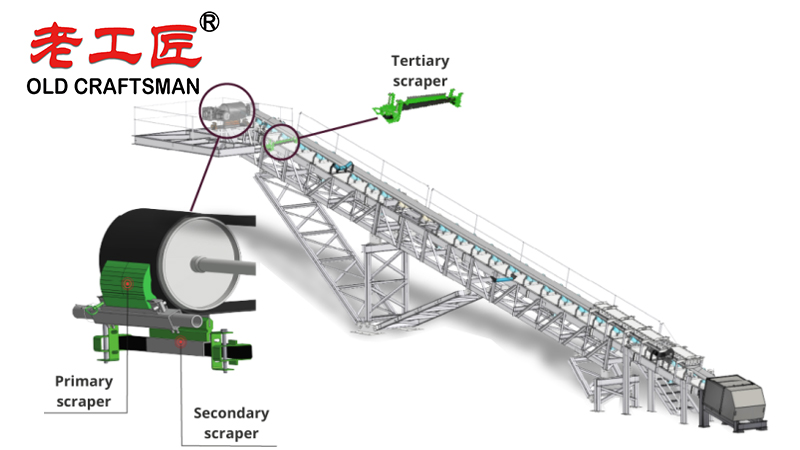
2. Extended Belt Life
- Leftover abrasive materials accelerate belt wear. A tungsten carbide secondary scraper minimizes carryback, reducing belt surface degradation and pulley damage.
- Prevents material buildup, which can cause misalignment and premature belt failure.
3. Reduced Maintenance & Downtime
- Tungsten carbide’s wear resistance (5-10x longer life than polyurethane or steel scrapers) means fewer replacements and less maintenance.
- Minimizes material spillage, reducing cleanup costs and conveyor downtime.
4. Cost Savings
- Though initially more expensive, tungsten carbide scrapers outlast alternatives, lowering long-term operational costs.
- Reduces energy waste by preventing belt drag from residual material.
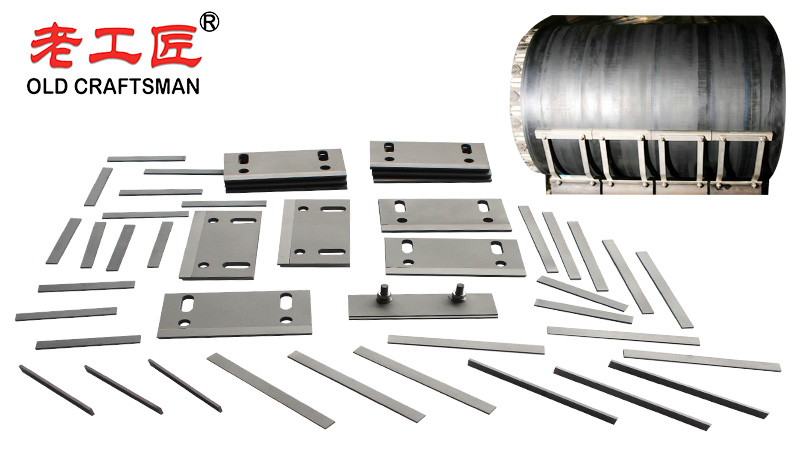
5. Performance in Harsh Conditions
- Ideal for wet, corrosive, or high-abrasion mining environments (e.g., coal, iron ore, limestone).
- Resists chemical degradation and maintains sharpness longer than softer materials.
6. Environmental & Safety Benefits
- Less carryback means fewer airborne dust particles, improving air quality and compliance with safety regulations.
- Reduces slip-and-fall hazards from spilled material.
Key Takeaway
A tungsten carbide secondary scraper is a high-performance solution for mining conveyors, ensuring cleaner belts, longer service life, and lower operational costs—critical for high-throughput, abrasive mining applications.
Tungsten carbide secondary scrapers are the optimal choice for mining conveyor systems due to their unmatched wear resistance, efficiency in material removal, and long-term cost savings. They help maintain belt longevity, reduce maintenance, and improve operational efficiency in abrasive mining environments.
“Zhuzhou Old Craftsman Precision Alloy Co., Ltd. could make tungsten carbide wear parts and make your equipment use life is tens of times longer than before! We specialize in providing customized carbide wear products solutions to meet the demanding requirements of industries such as aerospace, automotive, mining, and precision machining.”
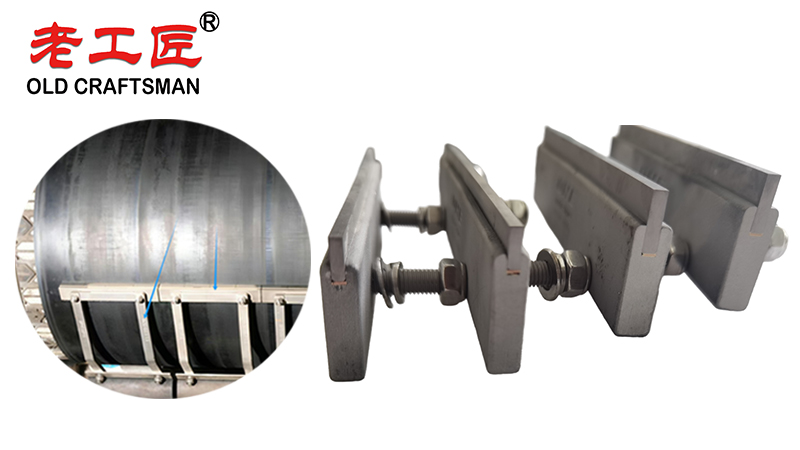
Blet scarper Brazing brazingprocess CARBDIE HAMMER carbide Carbide belt scraper carbidebrazing carbide hammer Crusher CRUSHER HAMMER Informational Internal stress metal mining mold operate Refractory Brick Mold Secondary belt cleaner scraper stresses VSI VSI crusher wear plates welding work