Mining conveyor systems often operate under harsh conditions, handling abrasive materials like ores, coal, and rocks. Tungsten carbide scrapers are widely used in these systems due to their exceptional durability and performance. Here’s why they are essential:
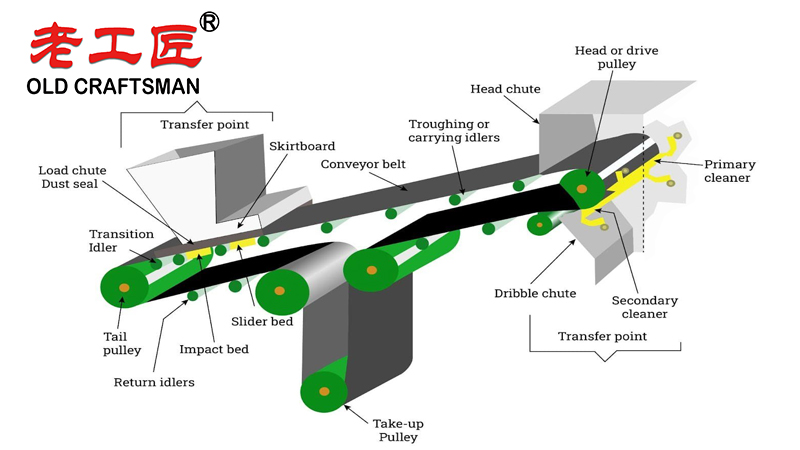
1. Extreme Wear Resistance
- Tungsten carbide is one of the hardest materials available (rated ~9 on the Mohs scale), making it highly resistant to abrasion from heavy, sharp, or gritty materials.
- Outlasts traditional steel or polyurethane scrapers by 5–10 times, reducing replacement frequency and downtime.
2. Enhanced Conveyor Belt Cleaning Efficiency
- The sharp, rigid edge of a tungsten carbide scraper ensures better cleaning of sticky or wet materials (e.g., coal slurry, iron ore fines).
- Prevents carryback (material sticking to the belt), reducing spillage and belt mistracking.
3. Cost-Effective in the Long Run
- Although more expensive upfront, tungsten carbide scrapers last significantly longer than alternatives, lowering maintenance and replacement costs over time.
- Reduces belt wear by minimizing abrasive material buildup, extending belt life.
4. Corrosion & Chemical Resistance
- Ideal for wet or chemically aggressive environments (e.g., mining with acidic runoff or saltwater exposure).
- Unlike steel, tungsten carbide does not rust or degrade easily.
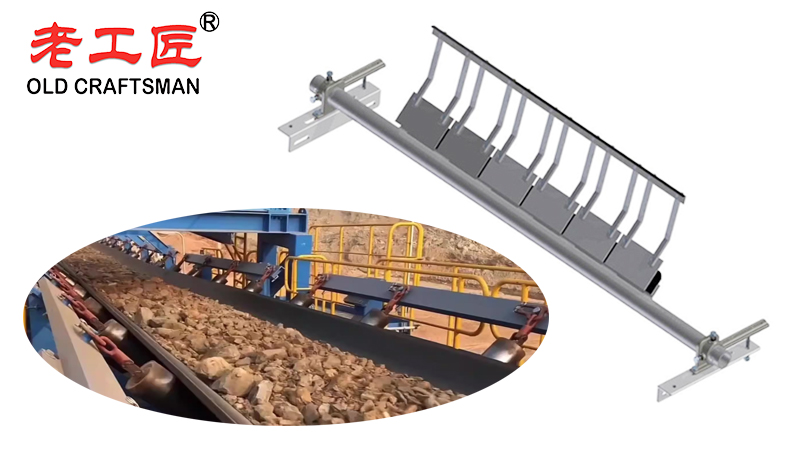
5. High-Temperature Performance
- Maintains hardness and structural integrity even in high-heat applications (e.g., conveying hot ash or sintered ores).
6. Reduced Energy Consumption
- Efficient scraping reduces belt drag, leading to lower power consumption for the conveyor system.
Common Applications in Mining:
- Primary & secondary belt cleaners on heavy-duty conveyors.
- Tail pulley scrapers to prevent material buildup.
- Transfer point cleaners to minimize spillage.
Comparison with Alternatives:
Material | Wear Life | Abrasion Resistance | Cost Efficiency |
---|---|---|---|
Tungsten Carbide | Very High | Excellent | Best long-term |
Steel | Low | Moderate | Frequent replacement |
Polyurethane | Medium | Good (soft wear) | Moderate |
Conclusion:
Tungsten carbide scrapers are the optimal choice for mining conveyor systems due to their unmatched wear resistance, efficiency in material removal, and long-term cost savings. They help maintain belt longevity, reduce maintenance, and improve operational efficiency in abrasive mining environments.
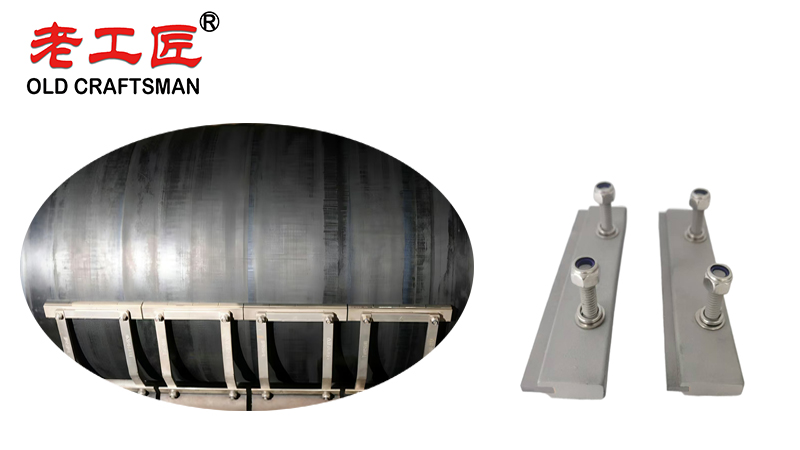
“Zhuzhou Old Craftsman Precision Alloy Co., Ltd. could make tungsten carbide wear parts and make your equipment use life is tens of times longer than before! We specialize in providing customized carbide wear products solutions to meet the demanding requirements of industries such as aerospace, automotive, mining, and precision machining.”
Blet scarper Brazing brazingprocess CARBDIE HAMMER carbide Carbide belt scraper carbidebrazing carbide hammer Crusher CRUSHER HAMMER Informational Internal stress metal mining mold operate Refractory Brick Mold Secondary belt cleaner scraper stresses VSI VSI crusher wear plates welding work